FLXO is a thinking tool for soft-robotics exploration. It's a platform consisting of modular interlocking pneumatic muscles that easily integrate with other robotics kits on the market. At present it's designed to integrate with the VeX robotics platform.
Role
Individual research project.
Research, design, engineering, prototyping, and presentation.
Research, design, engineering, prototyping, and presentation.
Tools and Technology
CAD modeling (Rhino)
Fabrication
3D printing (FDM and Polyjet)
Breadboard electronics and Arduino Programming
Fabrication
3D printing (FDM and Polyjet)
Breadboard electronics and Arduino Programming
FEATURED ON

Context
Soft robotics is an exciting and emerging field with a radically different approach to robotics, combining biomimetics and unconventional materials. Contrary to conventional robotics which employs rigid materials like metals and hard plastics, pneumatically or hydraulically actuated soft robots are squishy and highly adaptive to their surroundings. This makes them safe and ideal for collaborative work with humans and other organic life. Soft robotics has applications in industrial automation involving pick-and-carry operations on soft and fragile goods, prosthetics, surgical tools, search and rescue robots, and bio-mimetic design. Central to any soft robotic setup is soft actuators that work as engines for a given mechanism. You can think of these as soft and squishy motors without any moving parts!
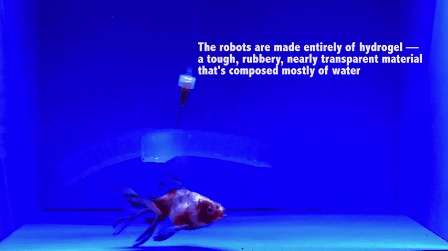
Challenge
This field is still in its infancy and there is yet a lot to be discovered and invented with a lot of promising applications in the future. There isn't enough accessible literature and documentation on the subject and a large part of the exploration takes place in well-funded research labs. The present approach to soft robotics involves fabricating soft actuators using silicone, hydro-gels or fabrics. Such actuators are usually designed for one time use with little to no affordances. The use or choice of soft materials also make them highly vulnerable to cuts and puncture and they start behaving unpredictably over time. At present anyone who wants to tinker with soft robotics needs to go through the tedious process of design, fabrication, and material sourcing which involves a lot of learning curves. This creates a bottle neck in open exploration of this technology.
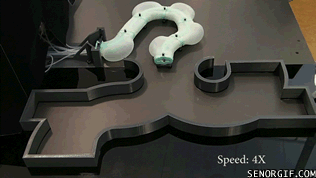

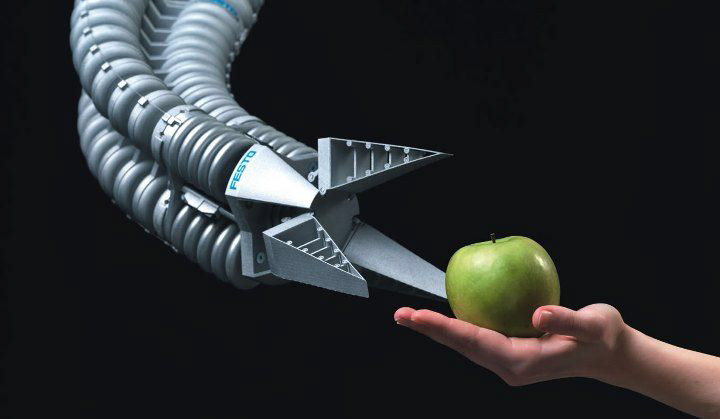
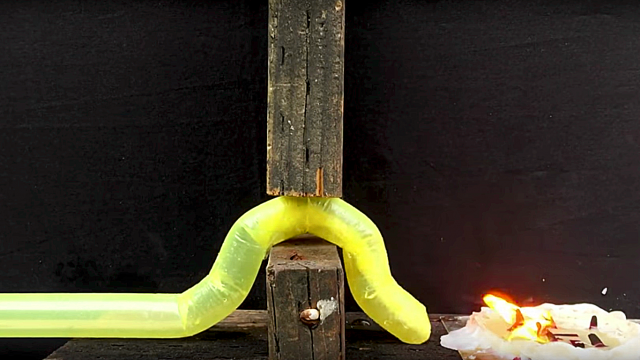
Target user persona
John is an electronics engineer/hardware designer and hobbyist tinkerer. He works at a product development company as a senior scientist. He is married and has two kids Elizabeth and Tim, Elizabeth goes to middle school and Tim is in high school. Elizabeth has an interest in biology and art and wants to pursue biomedical engineering. Tim is interested in pursuing industrial design after high school.
John has a good work-life balance and tries to spend enough time with his family. He takes an active interest in his kid's education and likes to teach them a variety of things and often takes them out to museums and art expos. He believes in a "learning-by-doing" approach and encourages his kids to explore the world outside of school, in a real context. Eight years ago he bought a 3D printer for the house and has several other educational toys around the house. He even has a small workshop in his garage where he spends time on the weekends, tinkering with new ideas. He also gives lectures as a guest sometimes in different art and design schools across the US.
John is a keen observer and maintains a sketchbook which he carries on him everywhere he goes. He always takes the subway to work and to get around in the city. In the summer months, the family often goes out on hikes and camping tours. Once a year they also take some time out to travel to a new place outside the country. John has been to over 26 countries so far.
His life goals include successfully running his design practice and going on to do bigger projects. Raising kids and providing them with good education and good values.
John has a good work-life balance and tries to spend enough time with his family. He takes an active interest in his kid's education and likes to teach them a variety of things and often takes them out to museums and art expos. He believes in a "learning-by-doing" approach and encourages his kids to explore the world outside of school, in a real context. Eight years ago he bought a 3D printer for the house and has several other educational toys around the house. He even has a small workshop in his garage where he spends time on the weekends, tinkering with new ideas. He also gives lectures as a guest sometimes in different art and design schools across the US.
John is a keen observer and maintains a sketchbook which he carries on him everywhere he goes. He always takes the subway to work and to get around in the city. In the summer months, the family often goes out on hikes and camping tours. Once a year they also take some time out to travel to a new place outside the country. John has been to over 26 countries so far.
His life goals include successfully running his design practice and going on to do bigger projects. Raising kids and providing them with good education and good values.
Use case
John recently got an inquiry for a new project that utilizes soft actuators for an assisted wearable suit. He has never worked with soft systems before so he is conducting basic desk research in his office on a quiet weekday afternoon. That’s when he comes across FLXO! The product claims to be a prototyping tool for soft systems. He finds the product introduction page on the website and learns of their prefabricated soft actuators that he can start to play with right off the box. The website also contains instructions and 3D CAD files of all the actuators which he can 3D print at home on his desktop 3D printer.
The kit has John feeling empowered to know that he can quickly prototype different actuators without needing to fabricate it himself, bringing him up to speed with the project.
The kit has John feeling empowered to know that he can quickly prototype different actuators without needing to fabricate it himself, bringing him up to speed with the project.
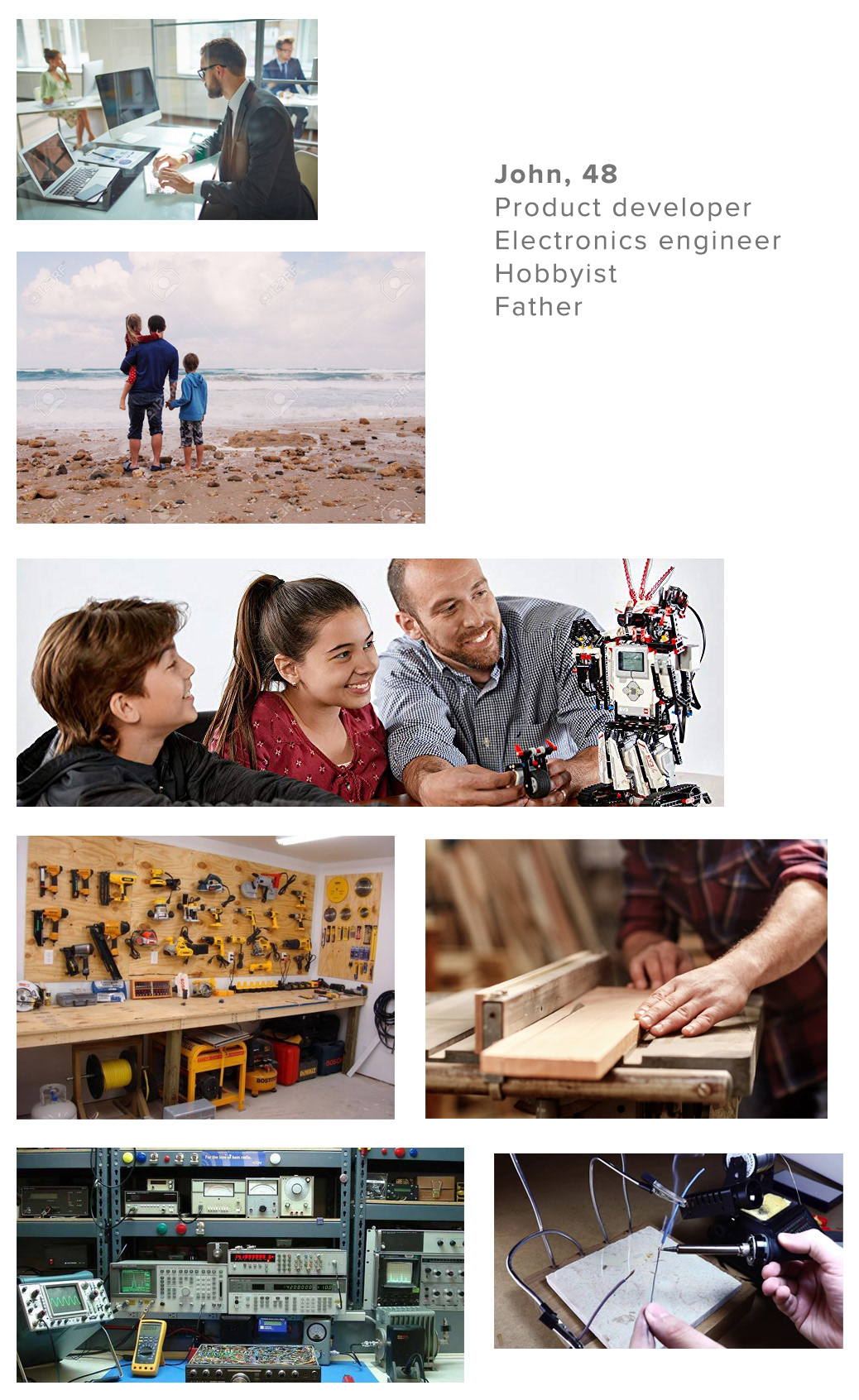
" I wanted to incorporate a soft gripper in one of my projects but didn't know how to make one. A ready-to-use kit would be really handy! " - Sam Chasan, Artist and coder
References and parallel products
I did a desk research on the current state of the art in soft robotics research. Below I've summarized key takeaways :
Applications
While really impressive, most of the research came out of well-funded research labs in elite institutions and was largely geared towards either search and rescue, surgical, pick and carry robots, or exoskeletons, and hence far from regular consumer use.
While really impressive, most of the research came out of well-funded research labs in elite institutions and was largely geared towards either search and rescue, surgical, pick and carry robots, or exoskeletons, and hence far from regular consumer use.
Materials
While the materials status quo is changing and moving towards more experimental material use, an overwhelming number of projects employ soft silicone materials which are not very durable outside of the lab.
Modularity
While I did see some examples of modular soft robots, most modules were designed for easy assembly and disassembly or for task-specific modularity, rather than for creative exploration, like Lego.
Opensource community
The website soft robotics toolkit is the only resource that has instructions on casting your own soft actuators, almost all based on silicone casting along with making your own pneumatic control boards. Unfortunately, the website has been inactive for a couple of years and it lacks diversity in projects, perhaps due to a high learning curve.
Hardware
Pneuduino and Programmable Air (used for this project) are great examples of open-source, readily available, Arduino based pneumatic air control units to power your soft robotics projects.
5 key questions to explore/address through my thesis:
1) How can we make a modular, plug-and-play system for rapid prototyping with soft actuators?
2) What is the mechanism for coupling the modular elements?
3) How can we simplify and standardize the fabrication process of soft actuators
4) How to design the modular elements so that they can be easily interfaced with external actuators like pneumatic, hydraulic, dielectric, and string-based?
5) How well can the components integrate with other existing robotics kits?
Solution
Flxo is an ongoing research project to address this need, built around three key objectives -
1) Democratizing key concepts in soft robotics
Creating components that serve to introduce the user to staple approaches within soft robotics like actuation and movement is achieved primarily through pneumatics.
Creating components that serve to introduce the user to staple approaches within soft robotics like actuation and movement is achieved primarily through pneumatics.
2) Designing prefabricated soft actuators
Design and engineering of pre-made and ready-to-use soft actuators which are durable and work repeatedly in a predictable way.
3) Modular with a plug-and-play approach
One should be able to use the same actuators, right off the box, in different configurations, much like LEGO or K'nex.
Shown on the right is an early visualization of this platform.
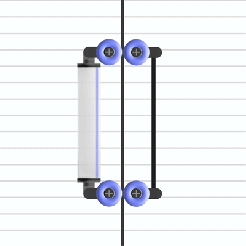
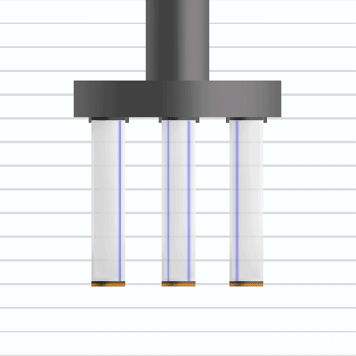
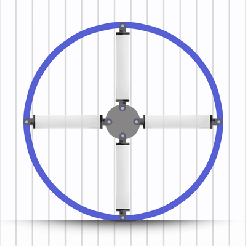
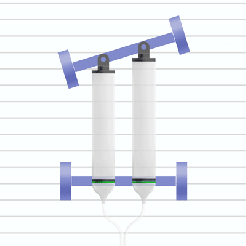
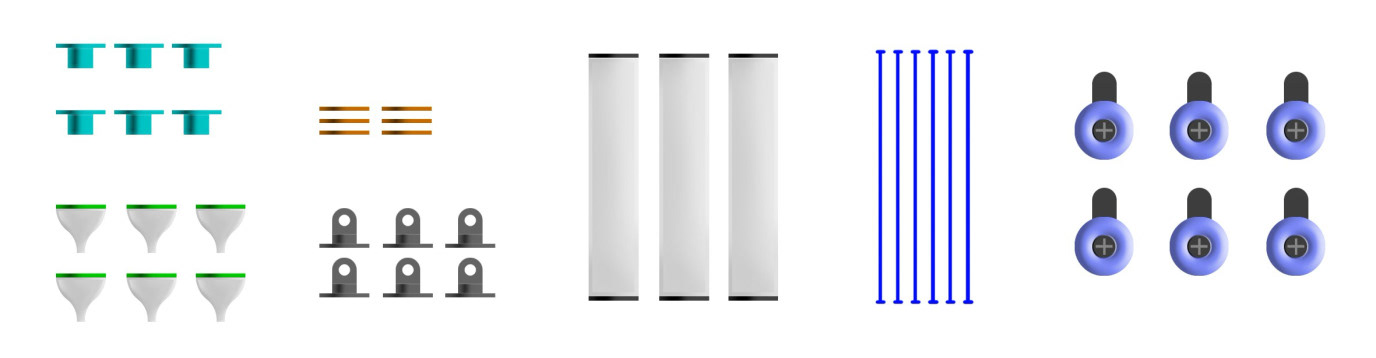
Approach
This project was divided into 2 phases
Phase 1:
Designing an optimum soft linear actuator that will work repeatedly in a predictable way.
Designing an optimum soft linear actuator that will work repeatedly in a predictable way.
Phase 2:
Designing the coupling adapters that will allow FLXO to be modular and also integrate with other robotics kits. I designed it to integrate with the VeX robotics platform for its more targeted application in innovative kits-based robotics.
Designing the coupling adapters that will allow FLXO to be modular and also integrate with other robotics kits. I designed it to integrate with the VeX robotics platform for its more targeted application in innovative kits-based robotics.
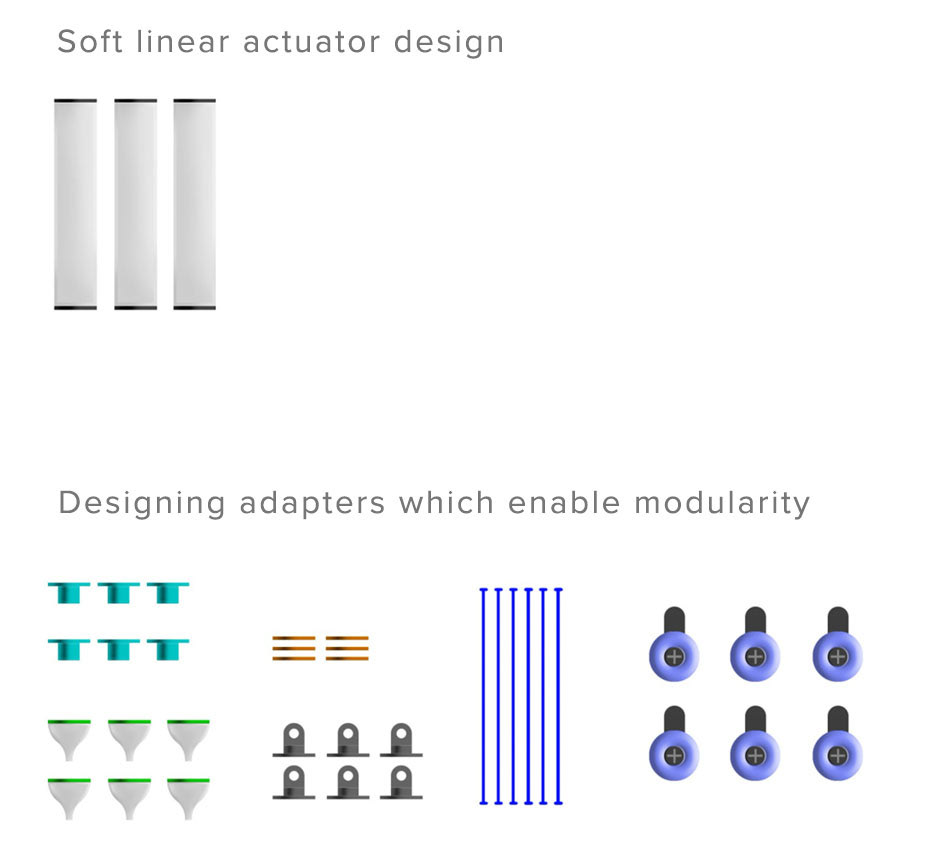
Design, fabrication, and testing
Version 1
Silicone 00-50 + 3D printed molds
Designed for positive air pressure (inflation)
Designed for positive air pressure (inflation)
I started off my design process by working with silicone, molding silicone structures with complex inner air channels and chambers. As you can see in the supporting gif animations, the result was far from satisfactory.
I encountered the following issues:
1) Did not produce the desired result.
2) The fabrication process was very labor-intensive and messy.
3) The results weren't exactly repeatable.
4) Lacked structural stability.
5) Vulnerable to cuts and punctures.
2) The fabrication process was very labor-intensive and messy.
3) The results weren't exactly repeatable.
4) Lacked structural stability.
5) Vulnerable to cuts and punctures.
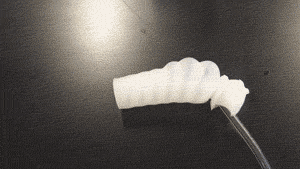
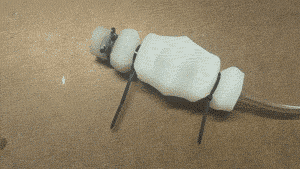
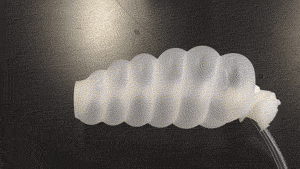
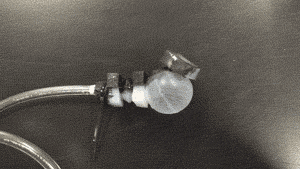
Version 2
Silicone 00-30 + thickener brushed on a piece of upholstery foam
Designed for negative air pressure (deflation)
Silicone 00-30 + thickener brushed on a piece of upholstery foam
Designed for negative air pressure (deflation)
For the second iteration, I decided to experiment with an inner core made of off-the-shelf upholstery foam and brushed thick silicone on top. This time I wanted to work with deflation as it is more organic and safer to control as opposed to inflation. Unfortunately, I yet again faced all the issues I encountered with the previous design. While user-testing the idea, I did receive very interesting comments from people!
" The texture is a little unsettling! " - Ari, Graphic designer
" It's weirdly flesh-like, can you not use silicone? " - Beverly Chou, Creative technologist
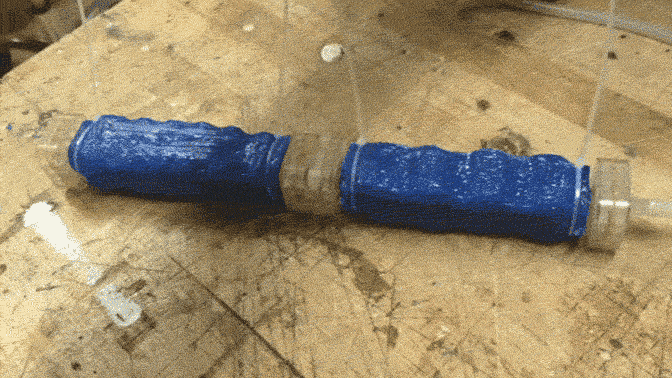
Version 3
3D printed origami? 🤔 🤑
I needed a radically new approach and I was thinking of ways to get rid of silicone altogether.
I finally thought of combining 3D printing and origami. The simple idea of 3D printing simple origami mechanisms in a flexible TPU filament produced very reliable soft actuators.
I finally thought of combining 3D printing and origami. The simple idea of 3D printing simple origami mechanisms in a flexible TPU filament produced very reliable soft actuators.
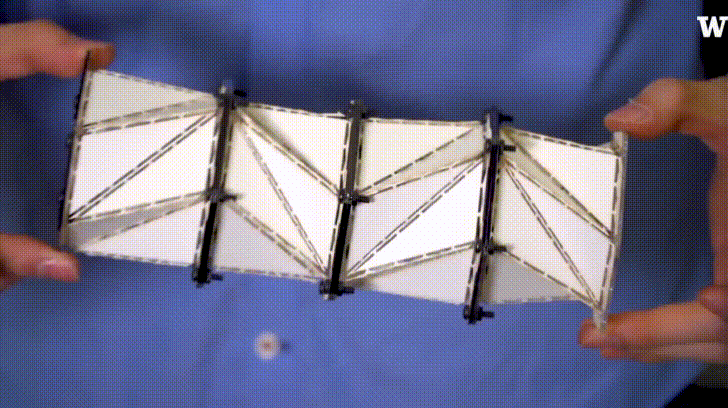
I researched several different origami/ bellow-inspired folding patterns and modified them as a single solid body in Rhino.
I also designed the coupling adapters in Rhino. These were to be 3D printed in Polyjet for high resolution.
After numerous iterations, I finally managed to work out the right wall thickness and print settings to achieve a clean print on the Ultimaker 3 with a dual extrusion head.
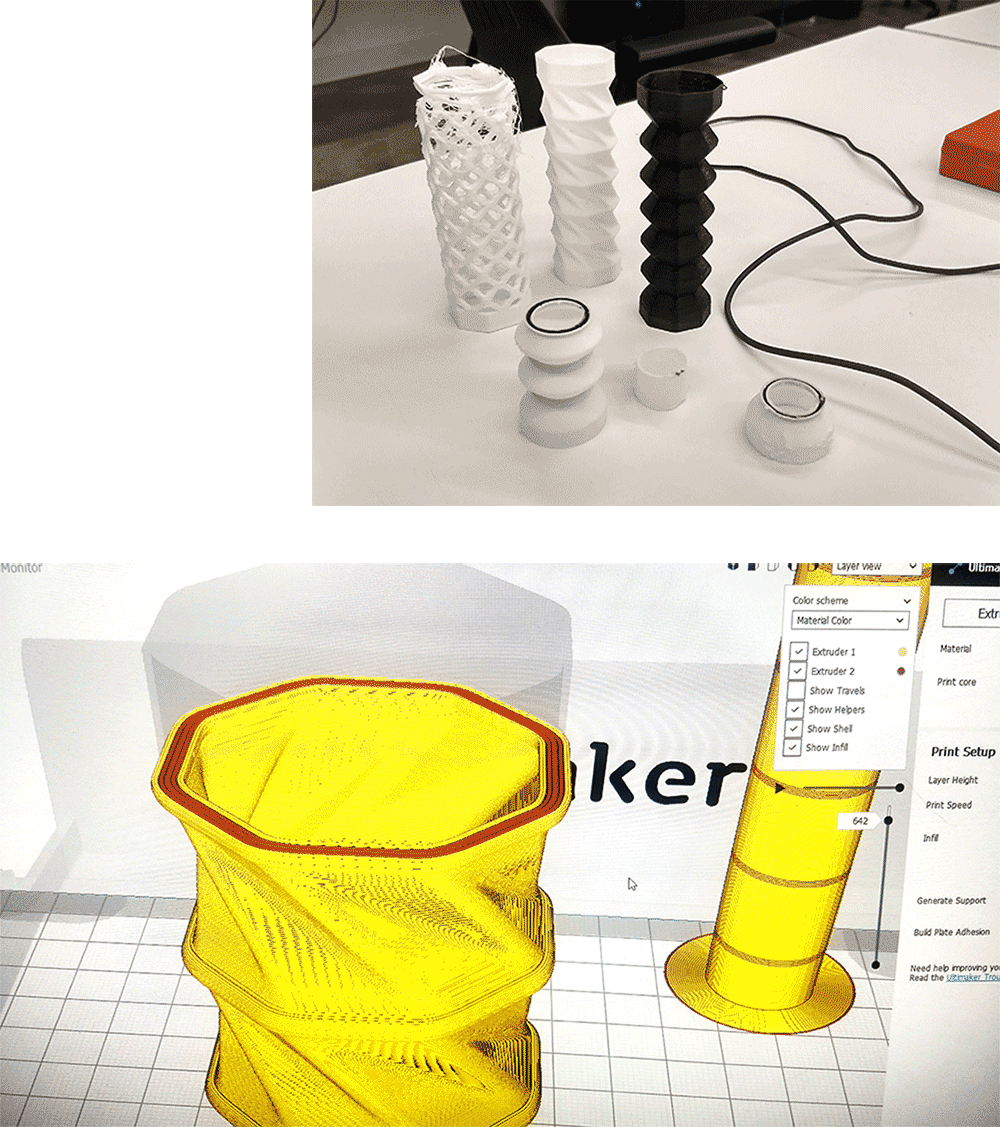
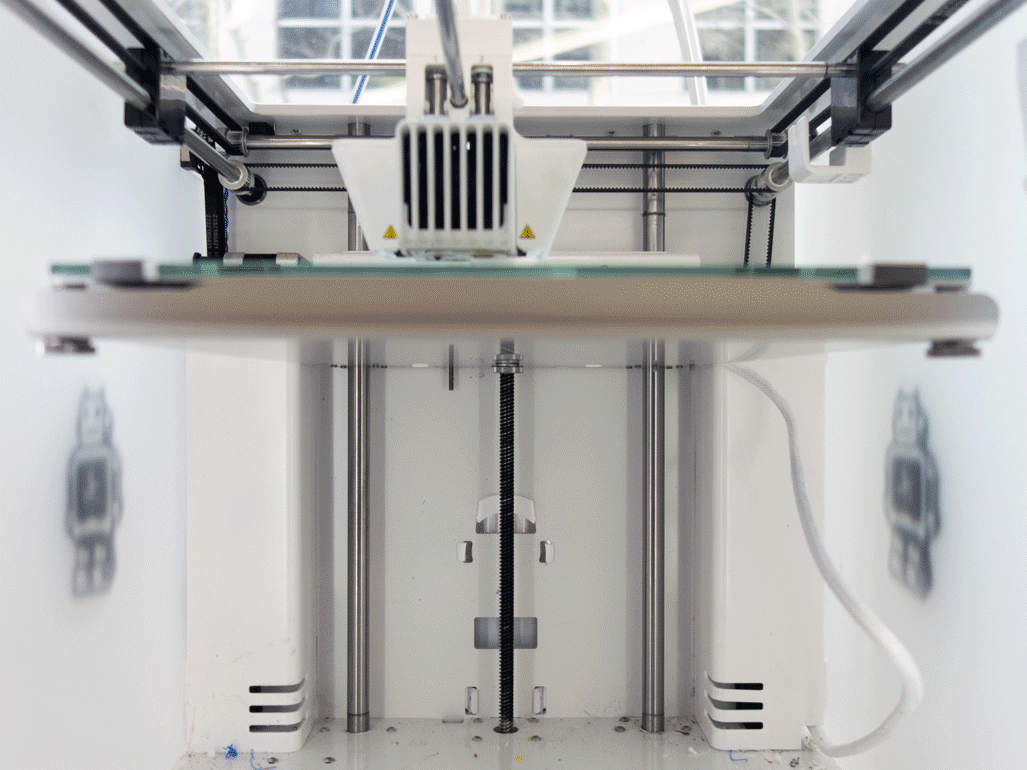
THESIS STATEMENT
FLXO merges origami folding and 3D printing to create robust soft actuators that seamlessly integrate with the VeX robotics platform. This kit enables effortless exploration of soft robotics, fostering democratic innovation and uncovering novel applications for this technology.
Shown below are the 4 different soft actuators. These are the basic building blocks that form an engine for a given mechanism.
The VeX robotics pieces easily snap into the soft actuators enabling rapid prototyping of hybrid, soft, and rigid robotic mechanisms. Below I've showcased some of my own examples of what is easily possible with this kit.
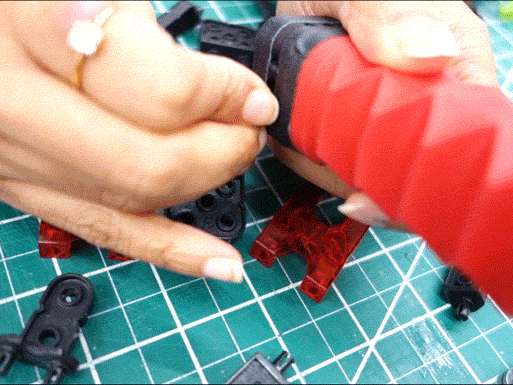

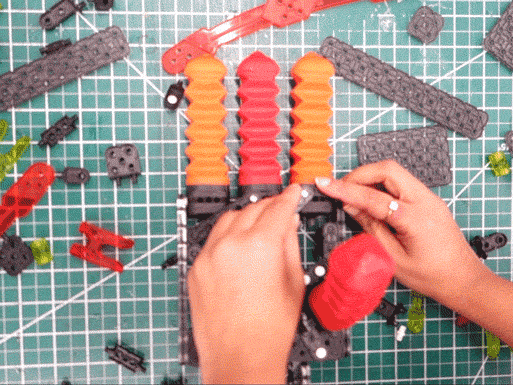
Why is this approach better?
1) This production method creates more reliable and durable actuators that work repeatedly in a predictable way.
2) The fabrication process is greatly simplified and cuts down on production time significantly. With this method, one can print and prep an actuator in less than 2 hours.
3) The resulting design is puncture and cut-proof.
4) They are rigid enough for structural integrity and squishy enough to be driven with just -6 Psi of pressure (cheap 12VDC air pumps).
5) The CAD files are easily modifiable and shareable over the internet.
2) The fabrication process is greatly simplified and cuts down on production time significantly. With this method, one can print and prep an actuator in less than 2 hours.
3) The resulting design is puncture and cut-proof.
4) They are rigid enough for structural integrity and squishy enough to be driven with just -6 Psi of pressure (cheap 12VDC air pumps).
5) The CAD files are easily modifiable and shareable over the internet.