Diamond Jewelry AUTHENTICATOR + IMAGING SOFTWARE
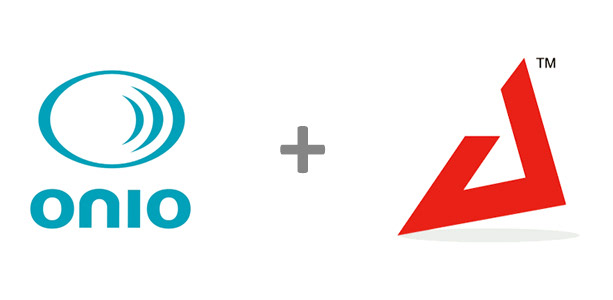
Background
I did this project while I was working at ONIO Design Pvt. Ltd. as an Industrial designer.
The product is launched in the market.
I did this project while I was working at ONIO Design Pvt. Ltd. as an Industrial designer.
The product is launched in the market.
Role
UXD, industrial design, CAD, assembly, fabrication, rendering, and presentation
UXD, industrial design, CAD, assembly, fabrication, rendering, and presentation
Client
DRC Techno is a subsidiary of Dharmanand Diamonds Pvt. Ltd., a leading global diamond manufacturer in Surat, India. DRC Techno specializes in product innovation and manufacturing of important instruments for the diamond and jewelry industry. From CNC diamond cutting machines to gemological research and development of accurate identification, evaluation, and assessment of diamonds.
DRC Techno is a subsidiary of Dharmanand Diamonds Pvt. Ltd., a leading global diamond manufacturer in Surat, India. DRC Techno specializes in product innovation and manufacturing of important instruments for the diamond and jewelry industry. From CNC diamond cutting machines to gemological research and development of accurate identification, evaluation, and assessment of diamonds.
Product
Synthetic diamonds or lab-grown diamonds are a serious threat to the diamond and jewelry industry. They cost about 30-40% less and are nearly identical to naturally occurring diamonds as the chemical composition is the same. This makes them show up as positive on diamond tester machines. To ensure safe and fair practices free of contamination in the diamond manufacturing to jewelry end-product pipeline, DRC pioneered a scanning instrument that can detect synthetic diamonds in all sizes (0.003 Cts - 10 Cts) and shapes.
Synthetic diamonds or lab-grown diamonds are a serious threat to the diamond and jewelry industry. They cost about 30-40% less and are nearly identical to naturally occurring diamonds as the chemical composition is the same. This makes them show up as positive on diamond tester machines. To ensure safe and fair practices free of contamination in the diamond manufacturing to jewelry end-product pipeline, DRC pioneered a scanning instrument that can detect synthetic diamonds in all sizes (0.003 Cts - 10 Cts) and shapes.
DRC was working on first-ever "mounted diamond jewelry detector". It can detect lab-grown diamonds from a set of mounted diamonds in necklaces, bangles, and rings.
Project goals and success metrics
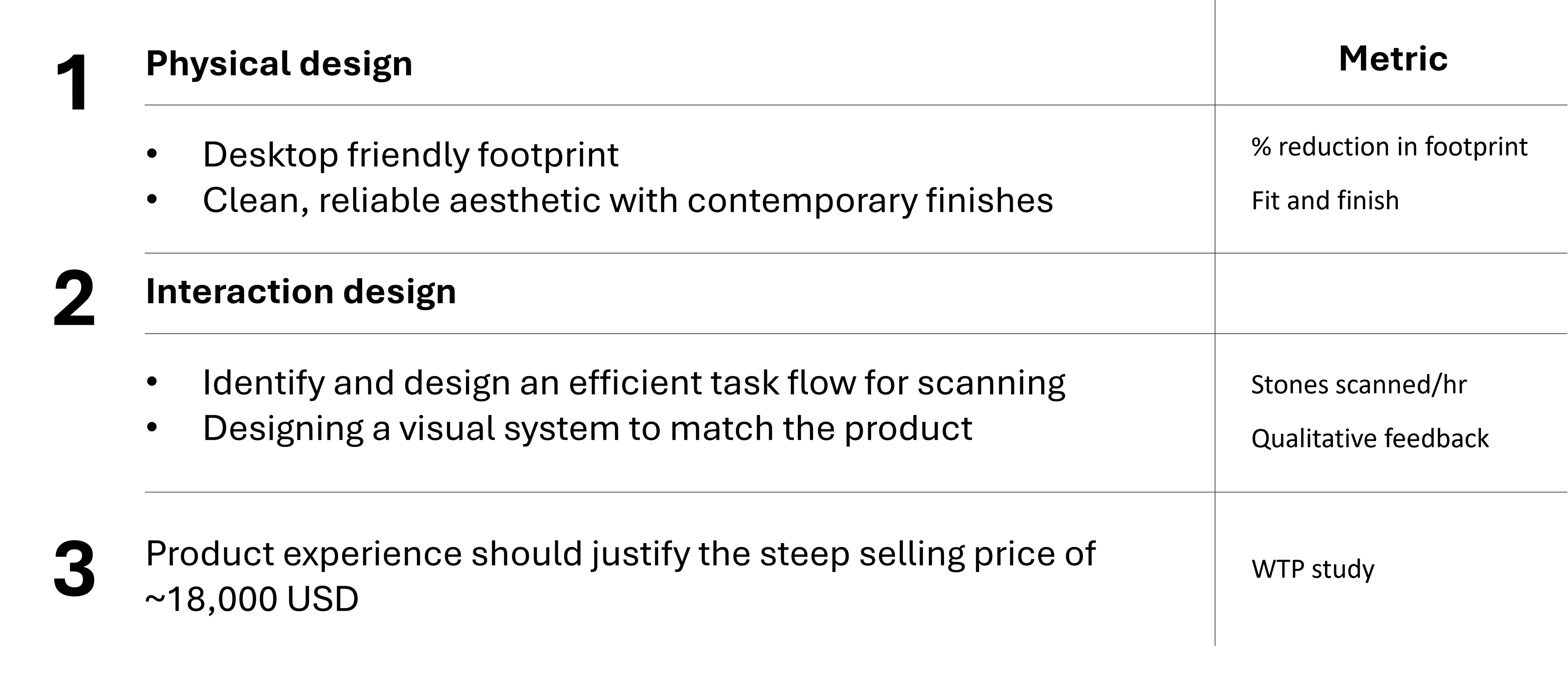
OUTCOME AND IMPACT
•Reduced machine footprint for a more desktop-friendly usage
•Significantly increased scanning volume
•Optimized the physical-digital workflow
•Reduced required hardware
•Created a visual UI kit for the client to build on for future versions
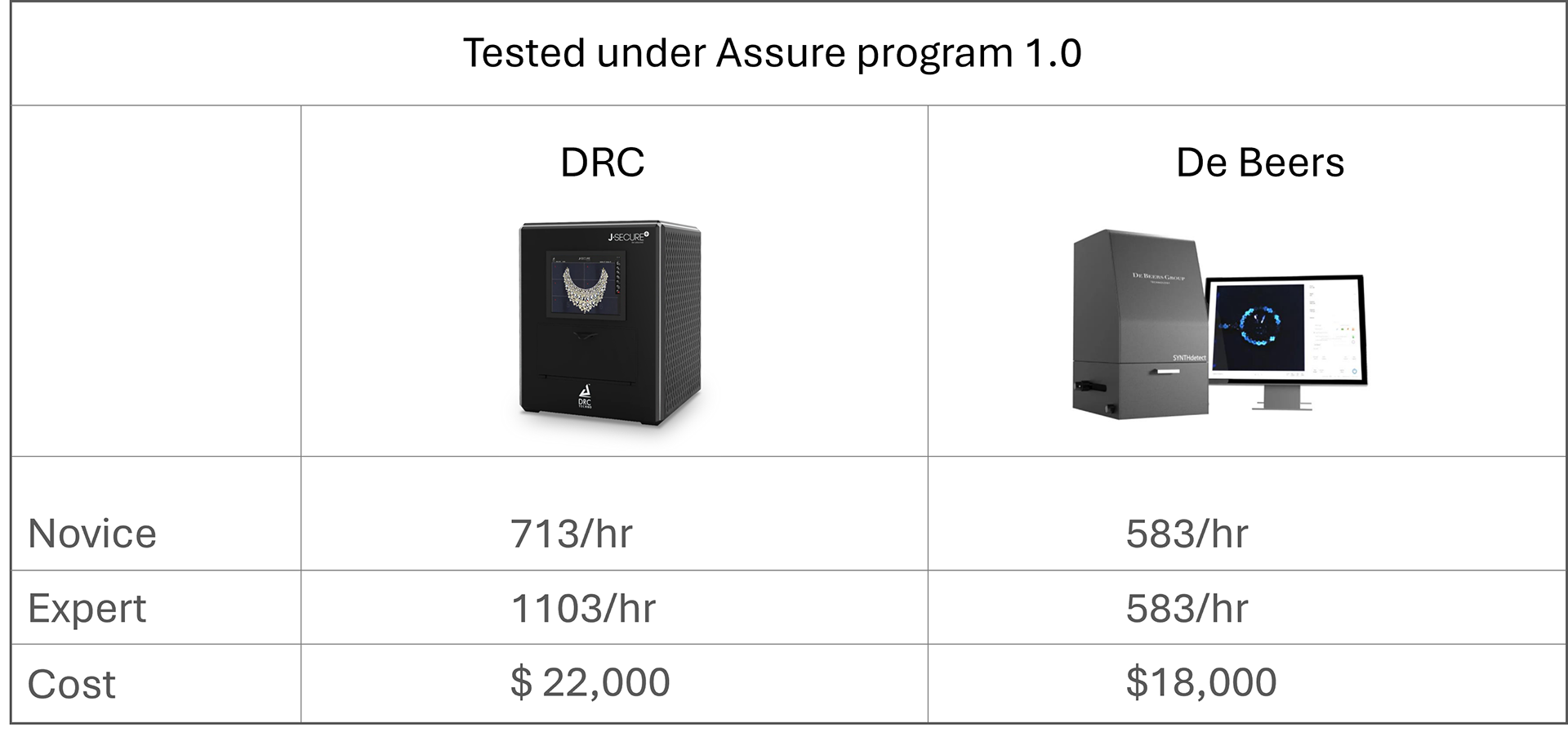
Challenge
DRC needed a well-stylized enclosure for their diamond jewelry scanner, J.Secure, and an unset diamond scanner, D.Secure, with the smallest possible footprint. The design language had to be consistent across varied enclosure dimensions. And also to redesign the imaging interface for the machine.
Client designed mechanism
DRC approached us with a prototype of the machine which was a simple arrangement of a scanning bed mounted on two X and Y-axis linear motors with an overhead camera.
The entire enclosure was about 3 feet X 3 feet X 3 feet and had to be mounted on a similar-sized pedestal with castors.
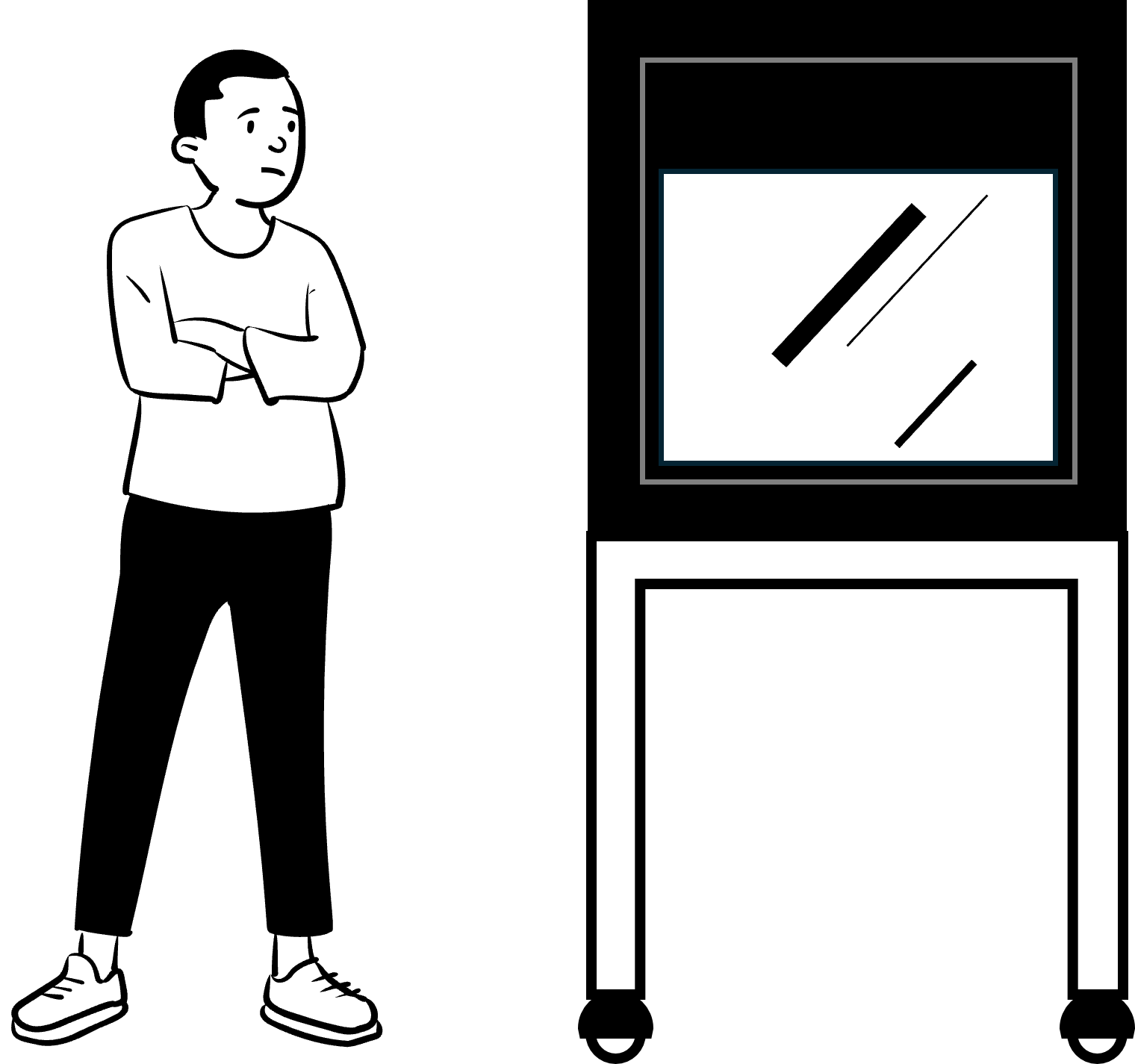
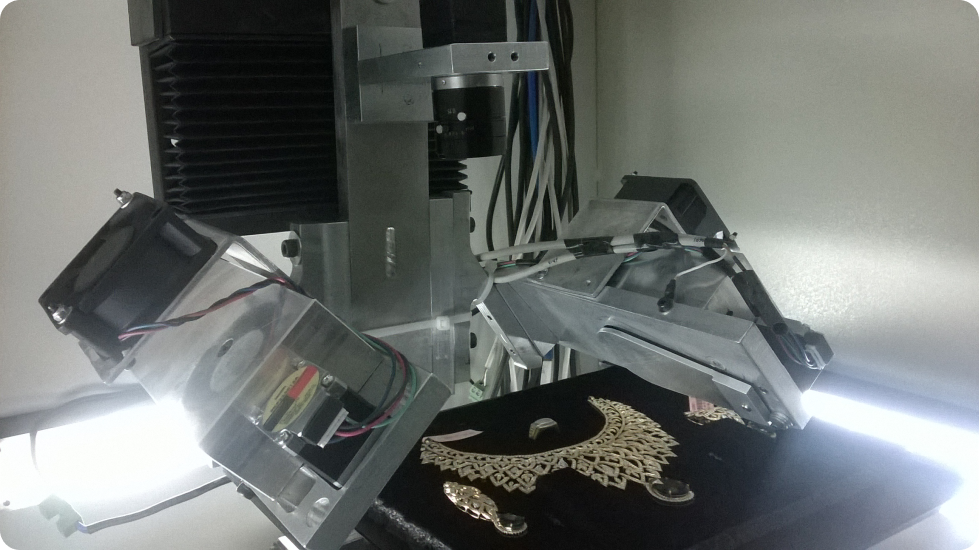
Client-side machine prototype
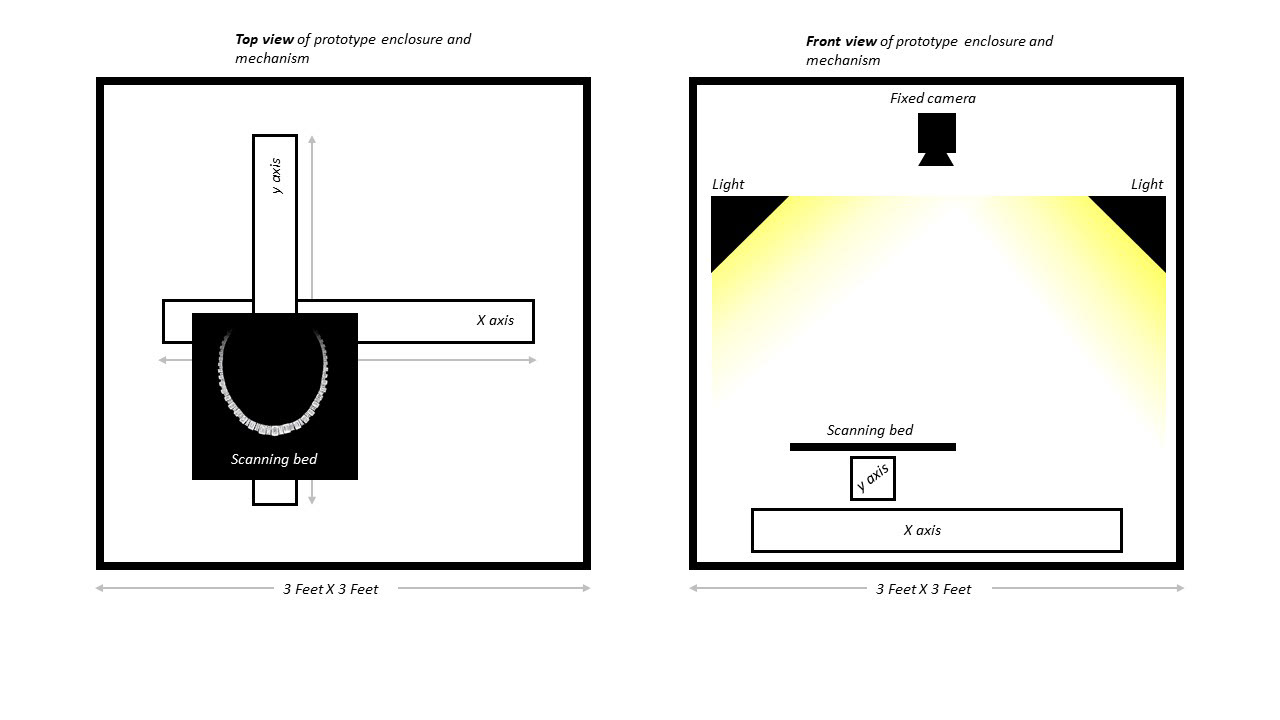
The choice of mechanism was simple and efficient from the point of view of standardization but needed too much space, substantially adding to the overall footprint of the enclosure. We envisioned the enclosure from the point of view of a desktop product that won't take up too much space in the busy offices and shops of diamond merchants in the Indian scenario.
Client-side interface
The client asked us to use the earlier D-Secure interface as a starting point. This interface was being used for their loose diamond scanning machine.
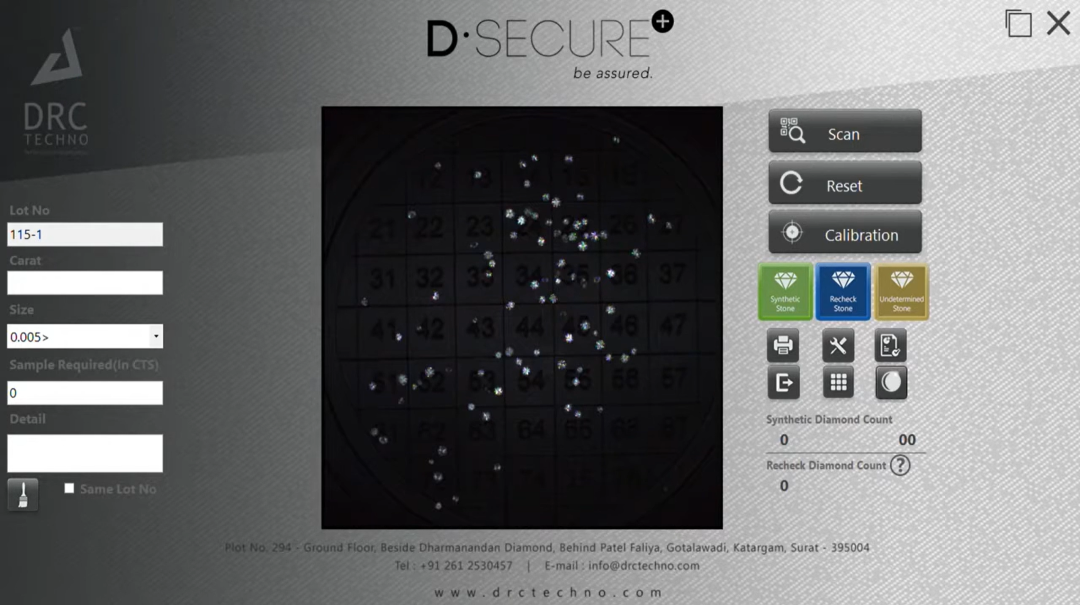
Client-side interface for loose diamond scanning machine
END CUSTOMER BACKGROUND
While the client only wanted us to quickly design a well-stylized enclosure, I couldn’t help but notice the massive footprint of the machine in the context of the end customer.
I identified two potential customer profiles for this machine, a diamond trader and a retail store, along with their respective needs and expectations from a machine like this.
I identified two potential customer profiles for this machine, a diamond trader and a retail store, along with their respective needs and expectations from a machine like this.
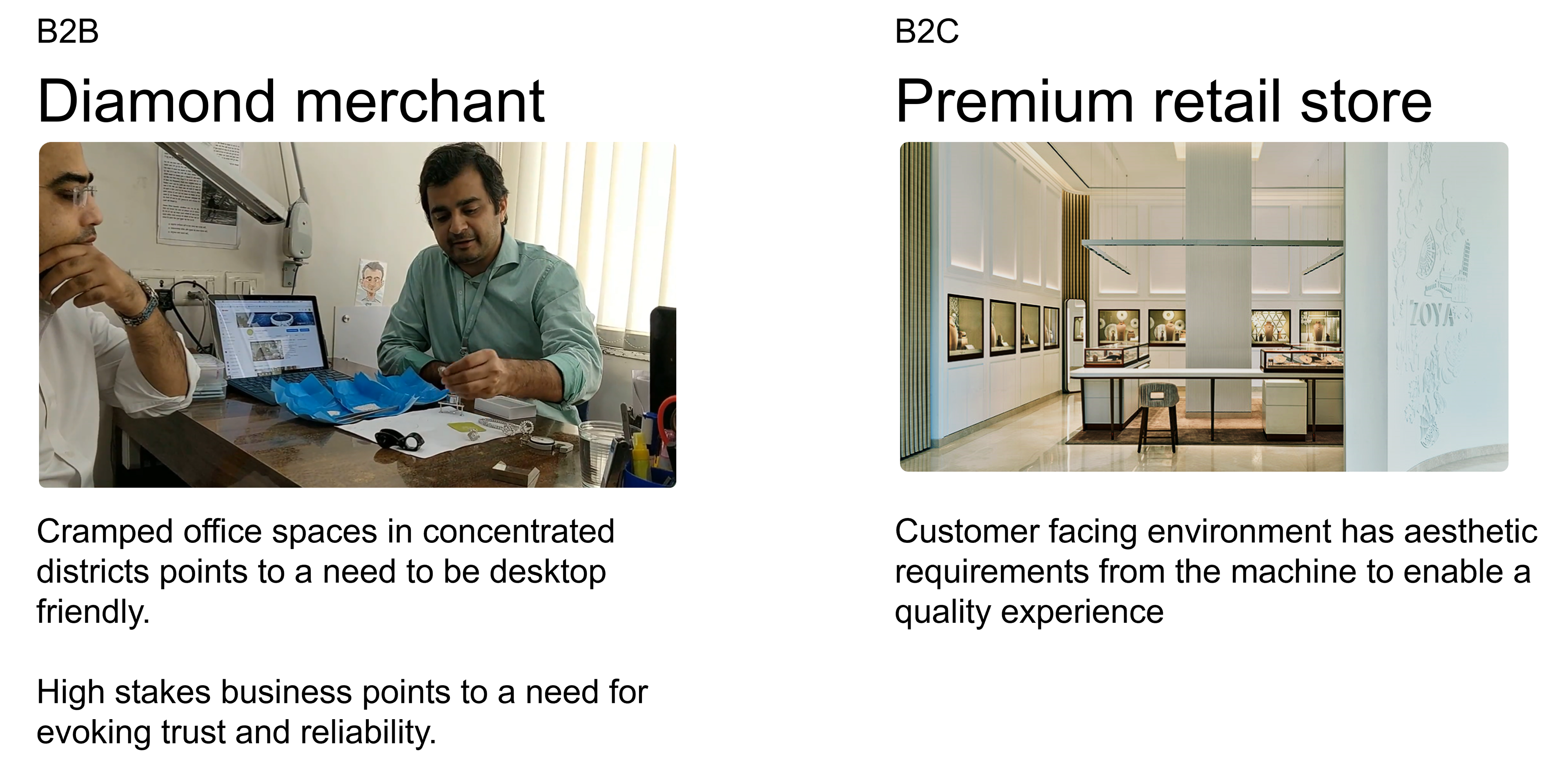
REDESIGNING THE HARDWARE SCHEMATIC AND MECHANISM
I proposed a different solution. Instead of mounting the scanning bed on the x, and y-axis, I instead chose to use a cylindrical shape for the scanning bed on a rotary axis. A cylindrical scanning prop leaned itself well to structured jewelry which would not rest completely on a flat scanning bed. The camera was mounted on a single z-axis. Just two axes were sufficient enough to cover the entire scanning area.
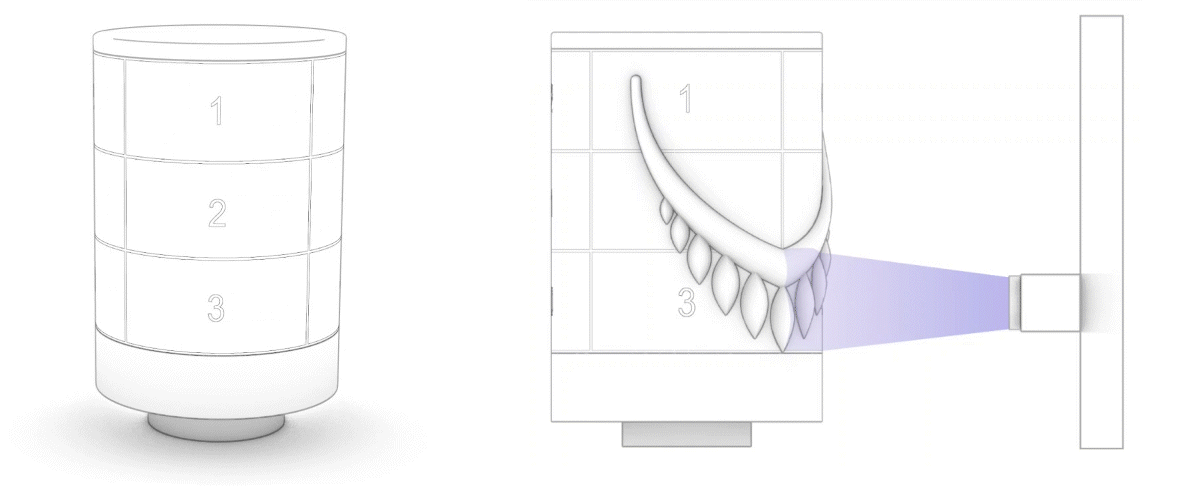
SIZING THE DISPLAY PROP AND DESIGNING THE GRID
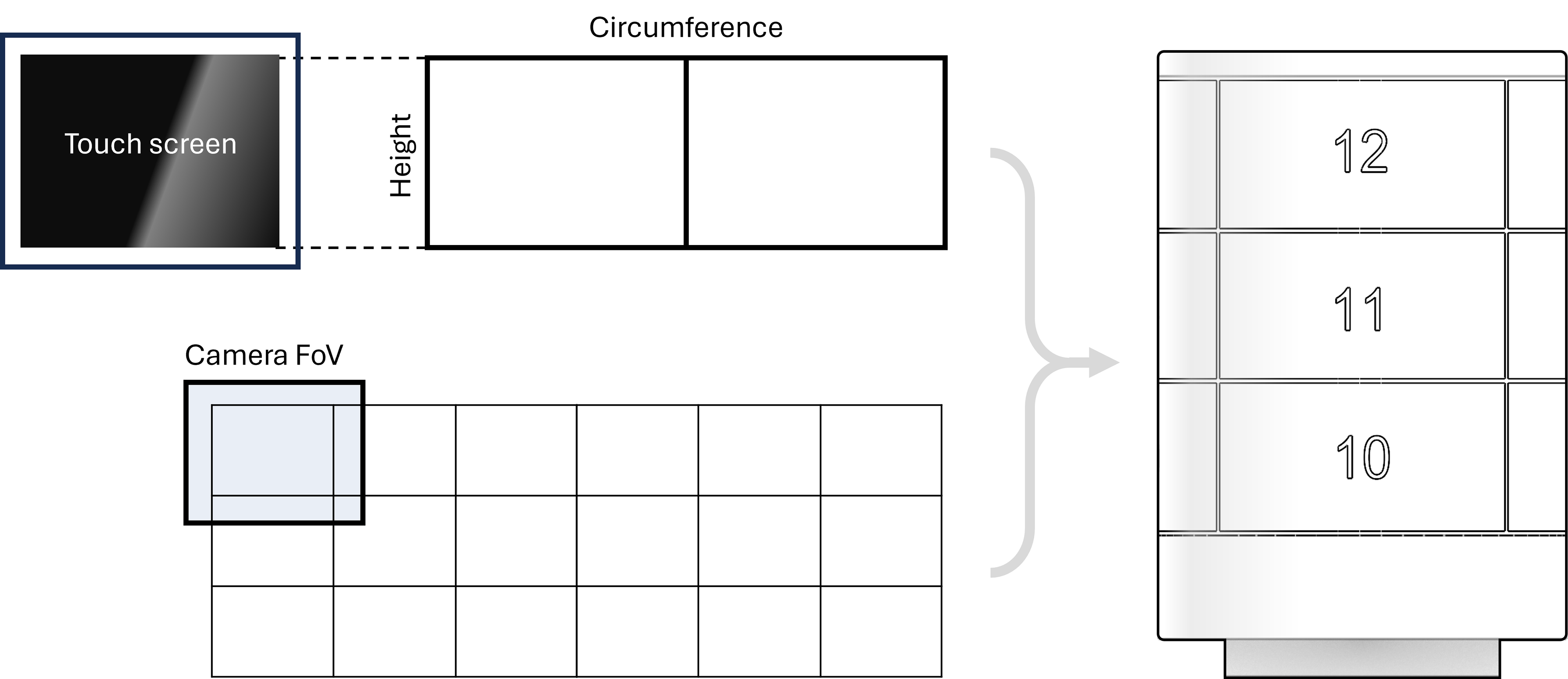
The next challenge was sizing the prop because the entire machine was essentially sized around that. At this stage, the client had identified a touch screen that was to go on the machine. The sizing of the prop was a function of the screen aspect ratio, so I could maximize the screen real estate when I displayed that prop on the interface.
And I also designed an appropriate grid system which was a function of the FoV of the scanning camera.
And I also designed an appropriate grid system which was a function of the FoV of the scanning camera.
PLANNING THE CAMERA MOVEMENT ALONG THE GRID TO COVER THE MAXIMUM AREA IN THE SHORTEST TIME
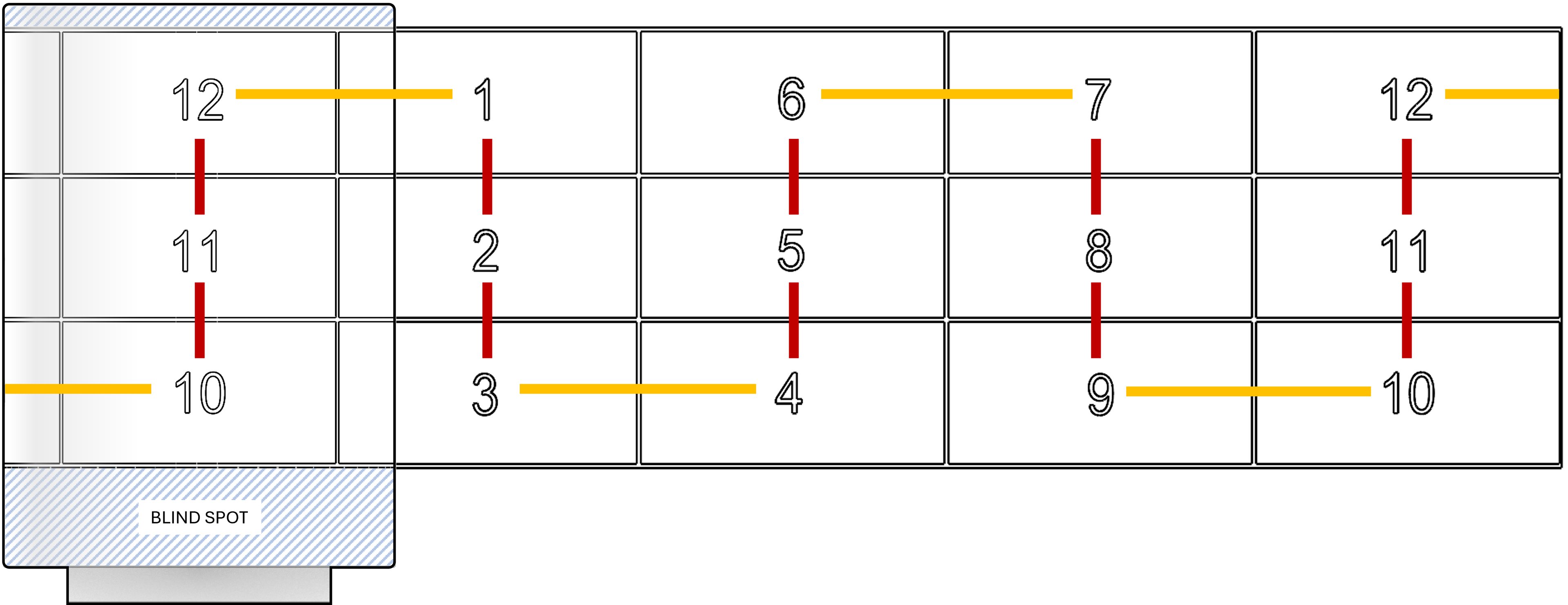
PROTOTYPING THE MECHANISM WITH ENGINEERS
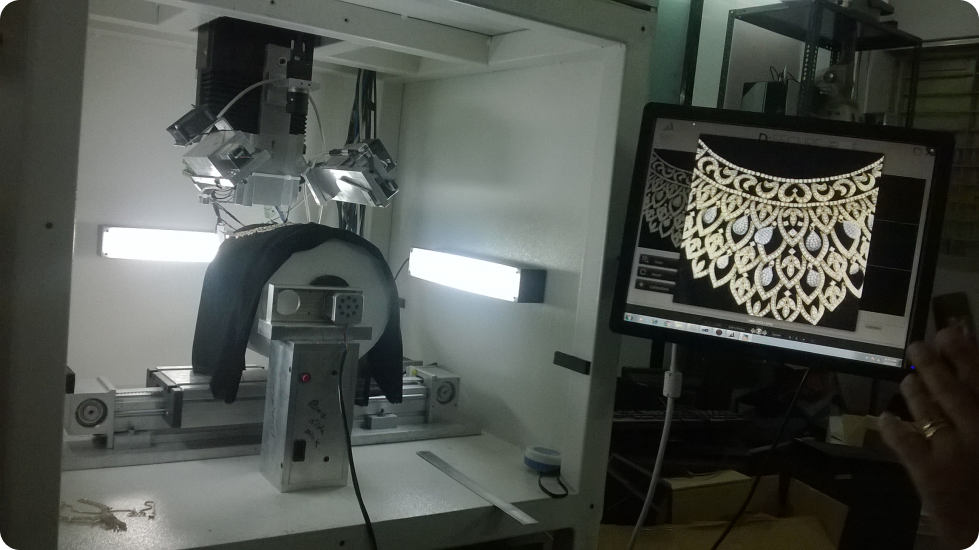
The redesigned schematic was prototyped on the client side for feasibility and it worked as expected!
The redesigned hardware schematic enabled the machine to be small enough to fit on a tabletop! My proposed mechanism achieved a 50% reduction in enclosure footprint, a 200% increase in the scanning surface area, and requiring 10% less hardware. This meant you could scan more jewelry in less time.
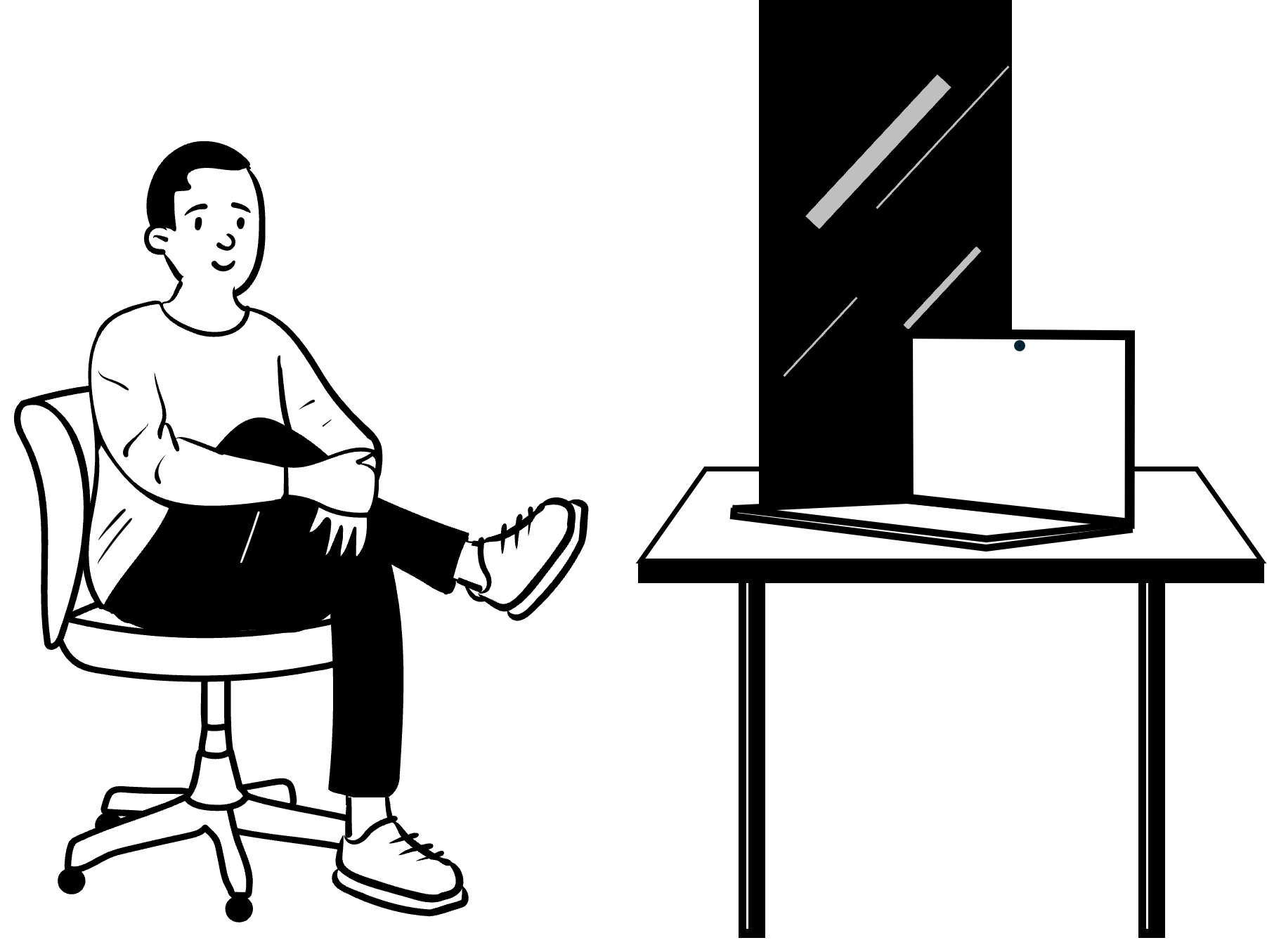
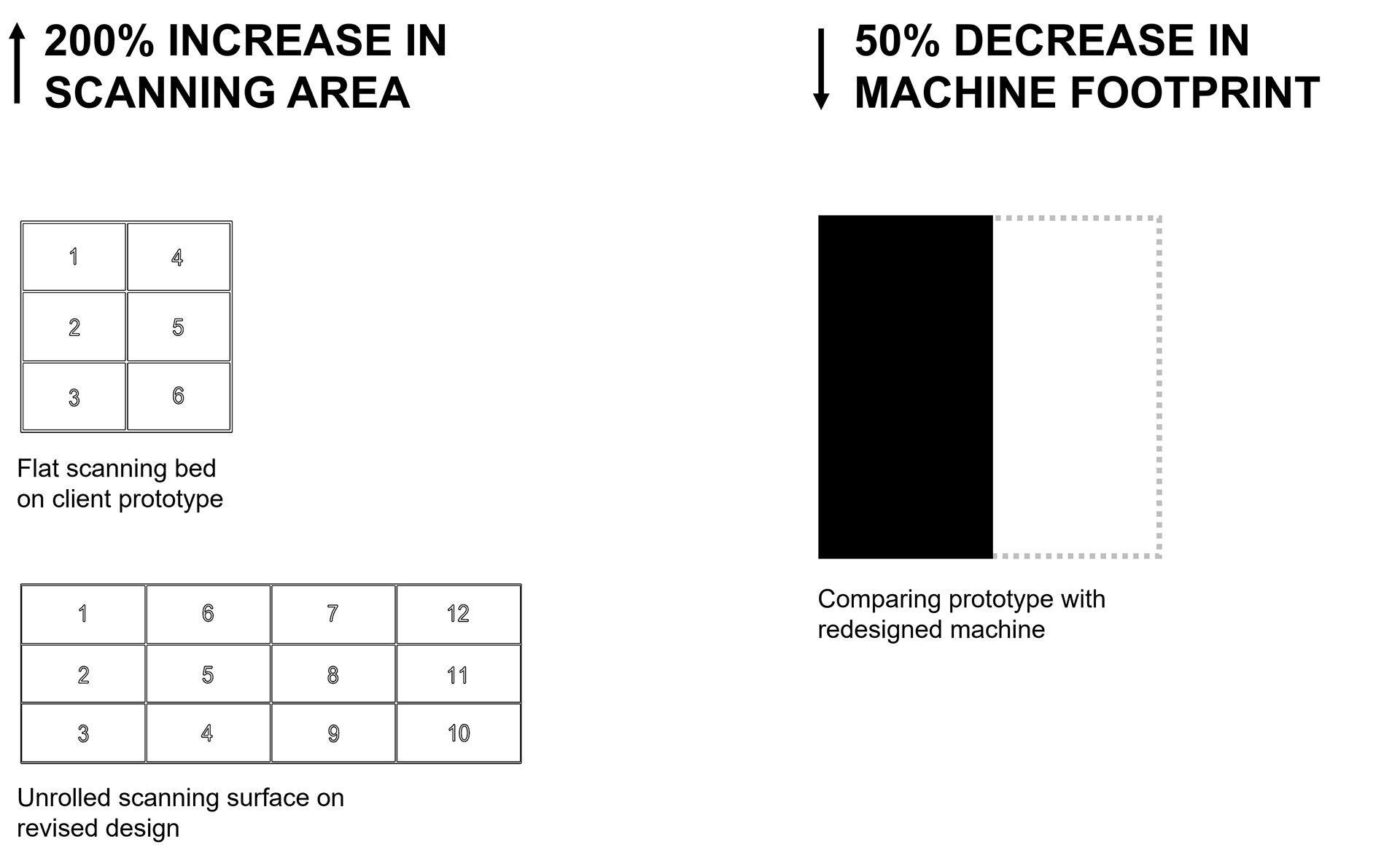
ENCLOSURE STYLING
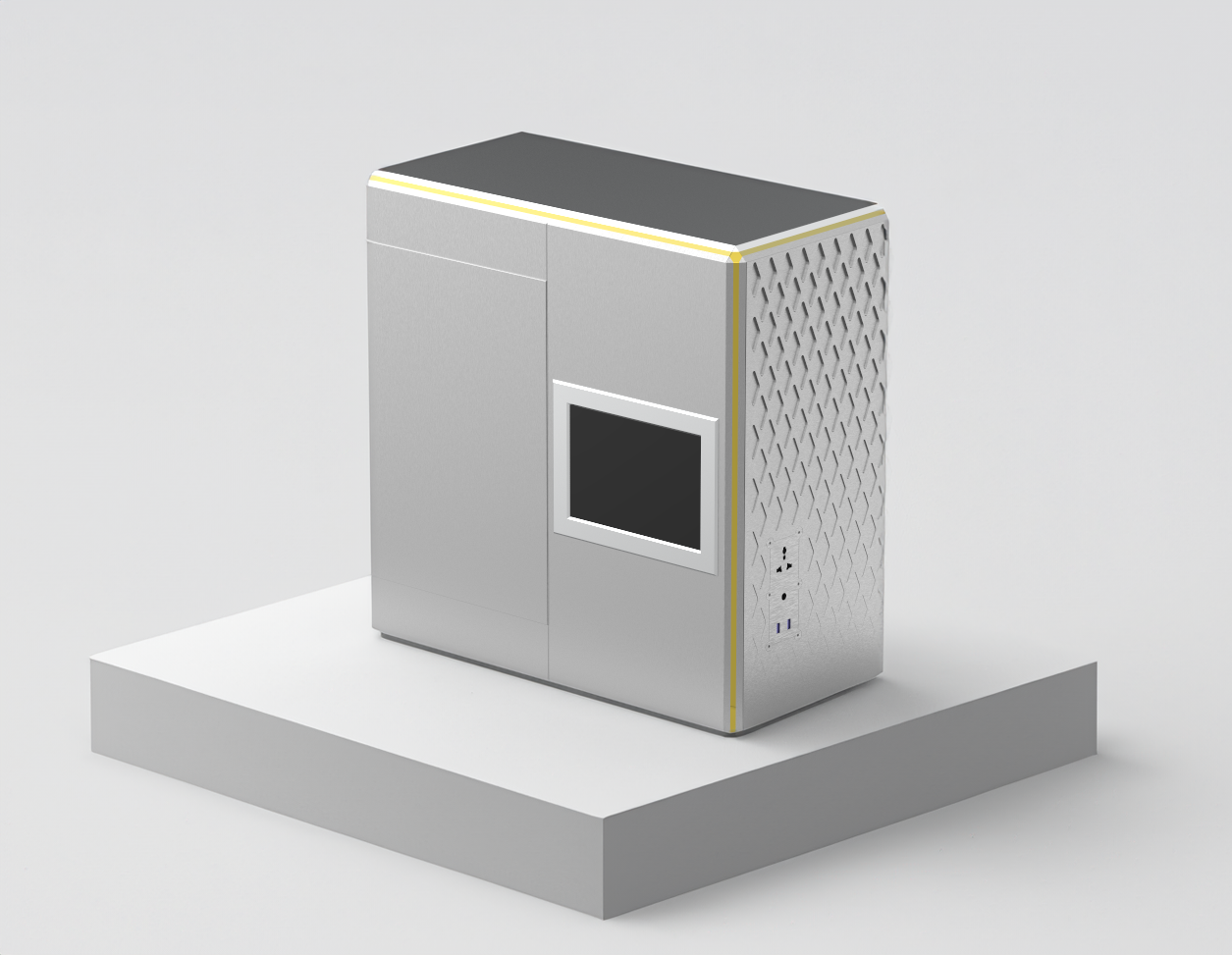
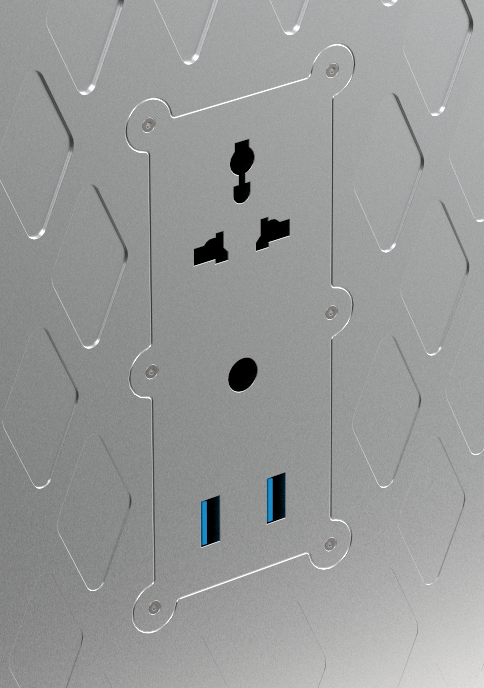
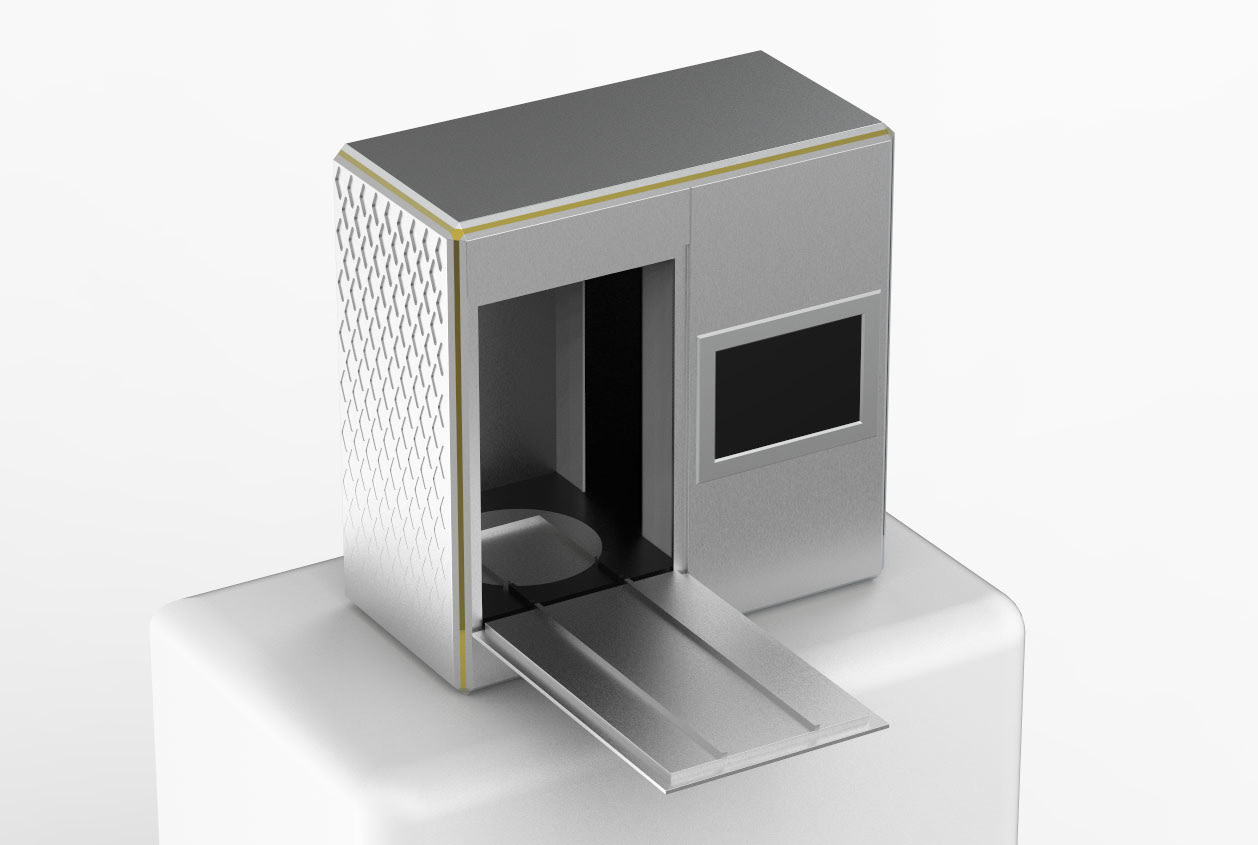
PROTOTYPE IMAGES
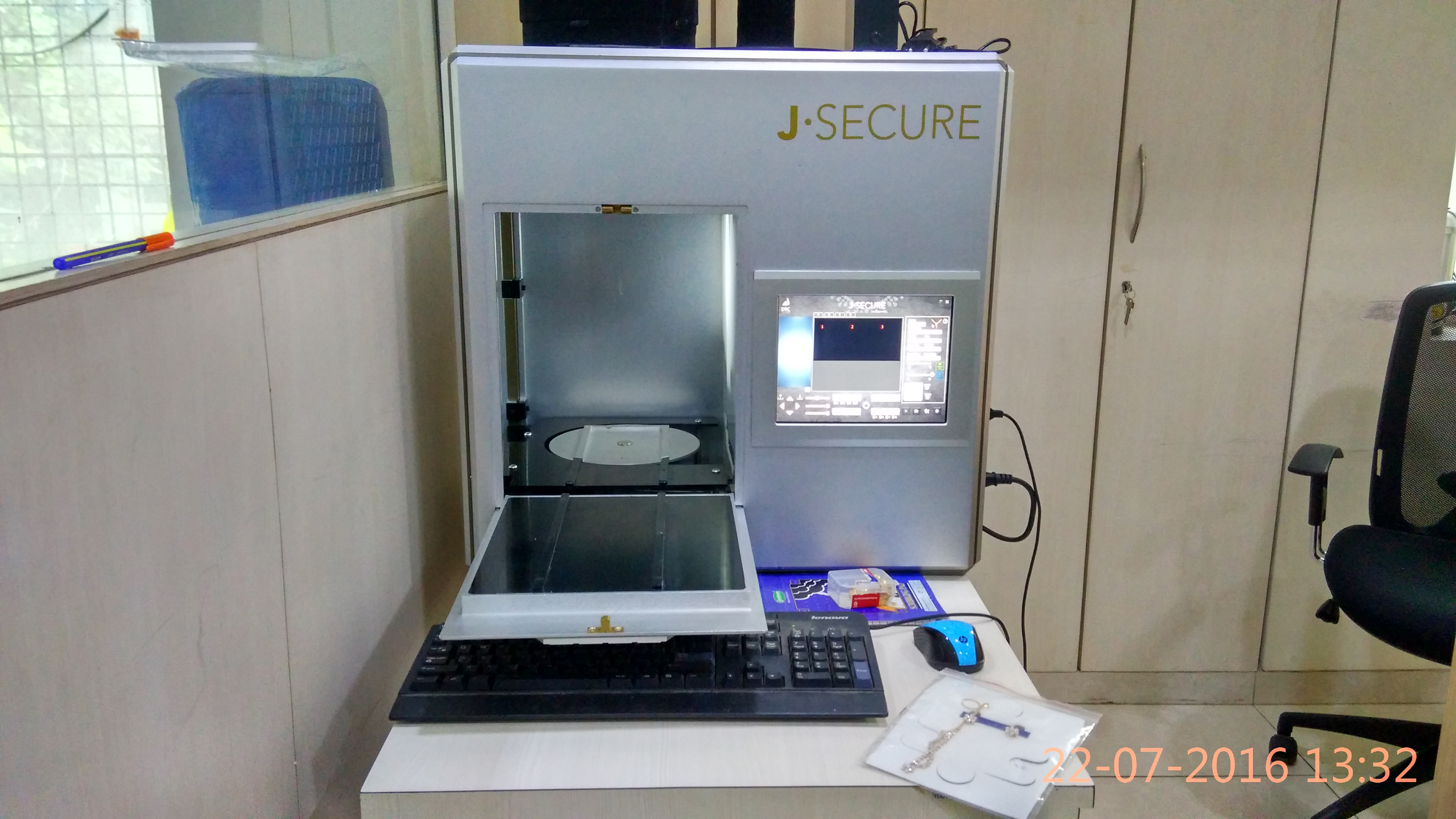
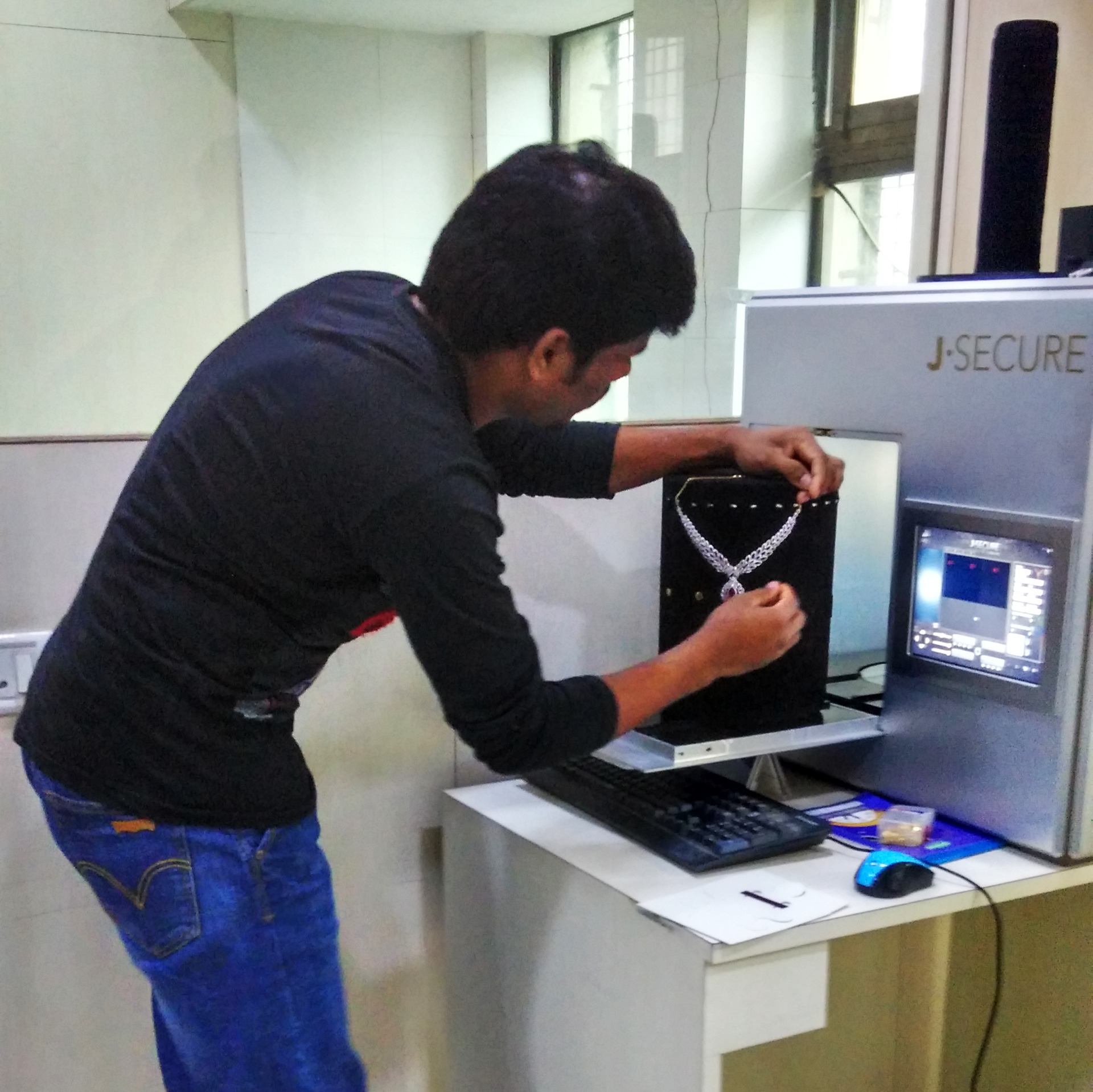
The entire enclosure was CNC milled in Aluminum with a premium anodized finish for longevity.
A custom-designed pattern was milled on the side panels to reflect the nature of the industry and customer affinity towards more ornamental styling.
A custom-designed pattern was milled on the side panels to reflect the nature of the industry and customer affinity towards more ornamental styling.
MY NEXT CHALLENGE WAS TO REDESIGN THE IMAGING SOFTWARE
I first did a UX audit of the interface and identified multiple issues with visual design and usability.
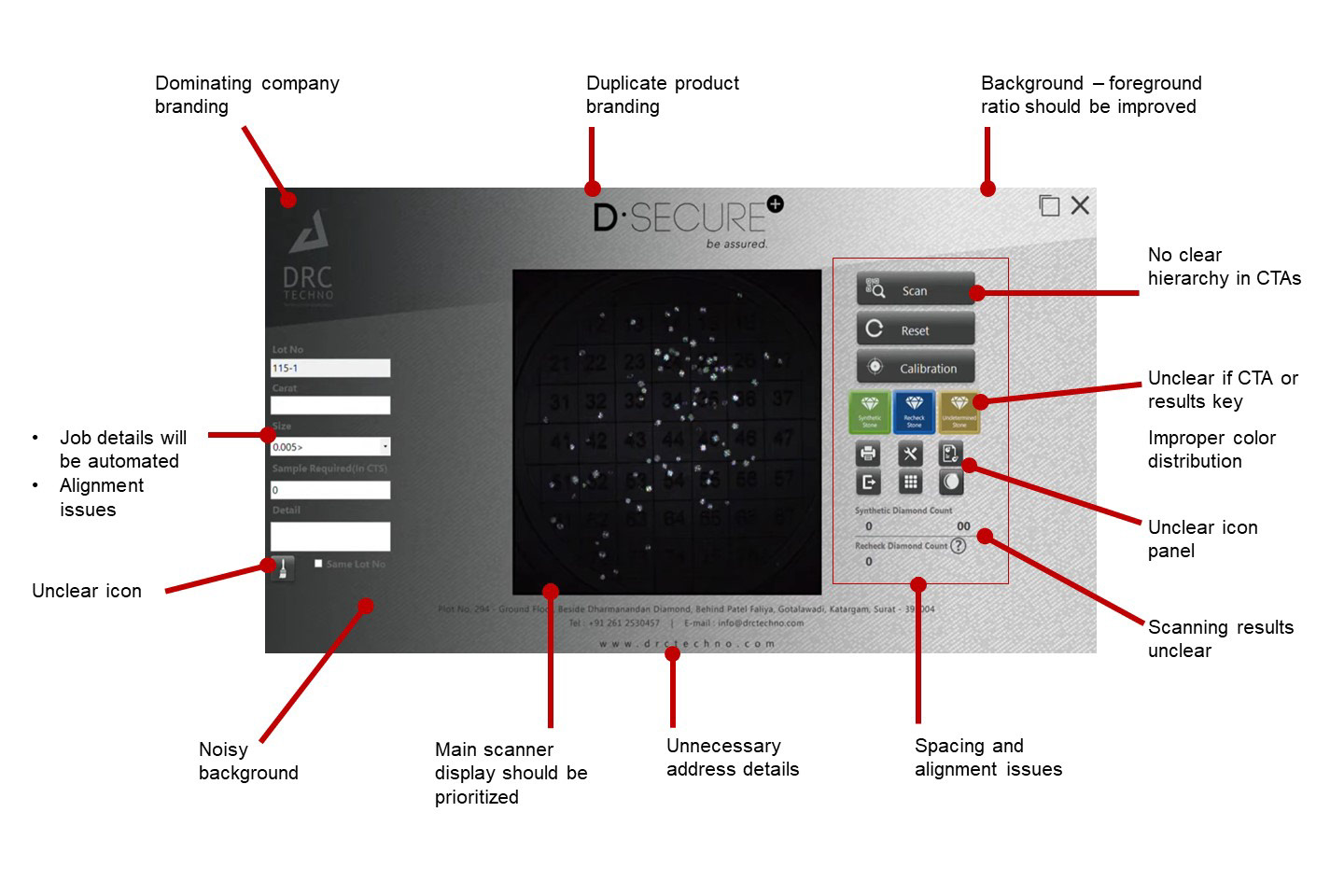
USE CASES
I worked with the marketing director on the client side to understand key customer use cases.
And we identified two main use cases which is buying and selling. While both use cases had similar processes, in the case of buying the focus is more on scanning and in the case of selling the focus is more on generating reports.
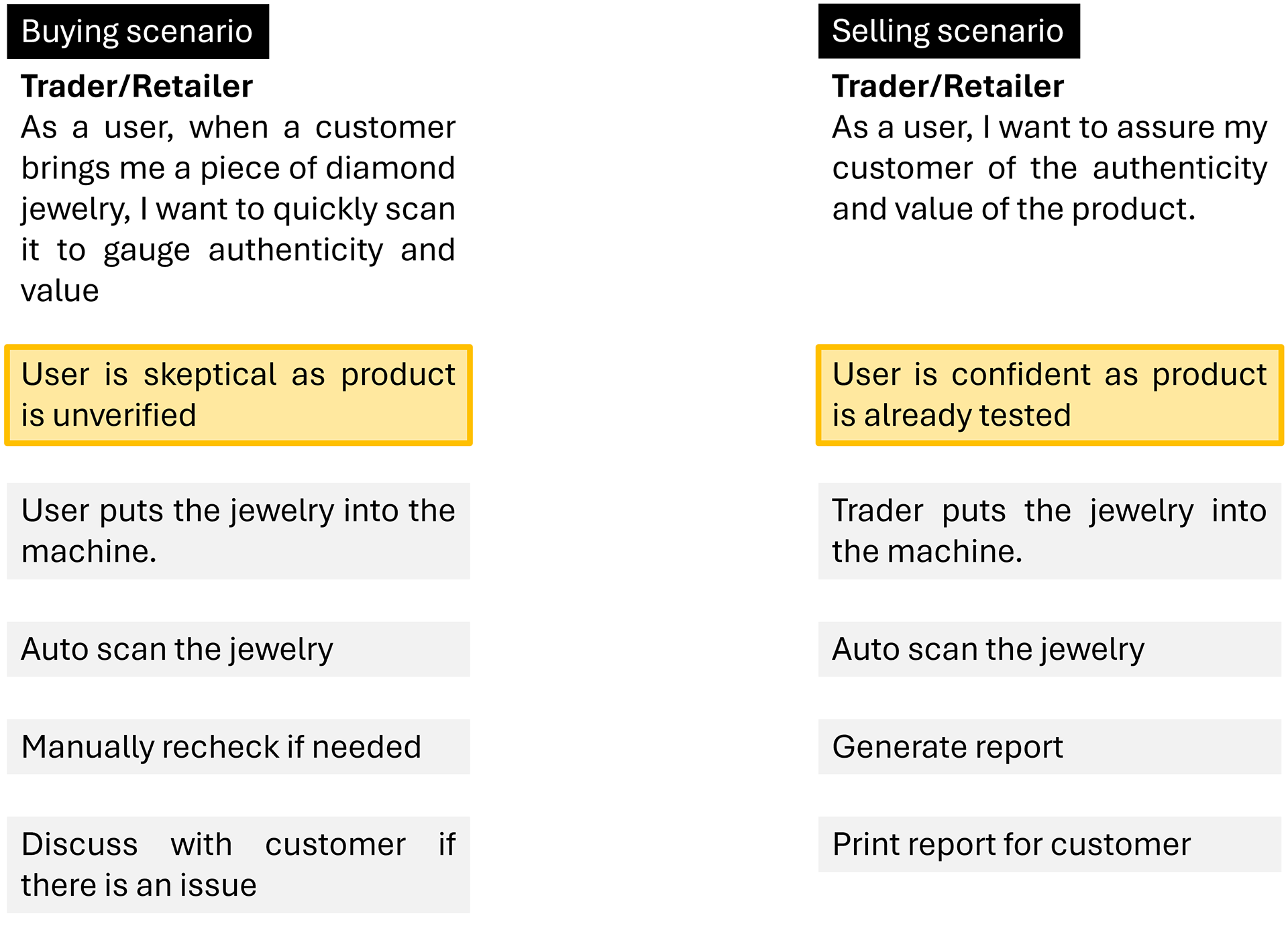
We identified some processes that were unique to this machine to the diamond scanner :
Intertwined physical and digital processes :
After the scan is completed, the user needs to pull out the prop and correlate the scan results with the jewelry placed on the prop.
Preview function:
Scan results can be of 3 types, all pass which is no cvd diamonds detected, some positives, and recheck.
Scan results can be of 3 types, all pass which is no cvd diamonds detected, some positives, and recheck.
In the case of recheck, when the jewelry is inserted back in for rescanning, the user may not want to auto-scan the whole prop but instead jump to a specific point on the grid and only scan that.
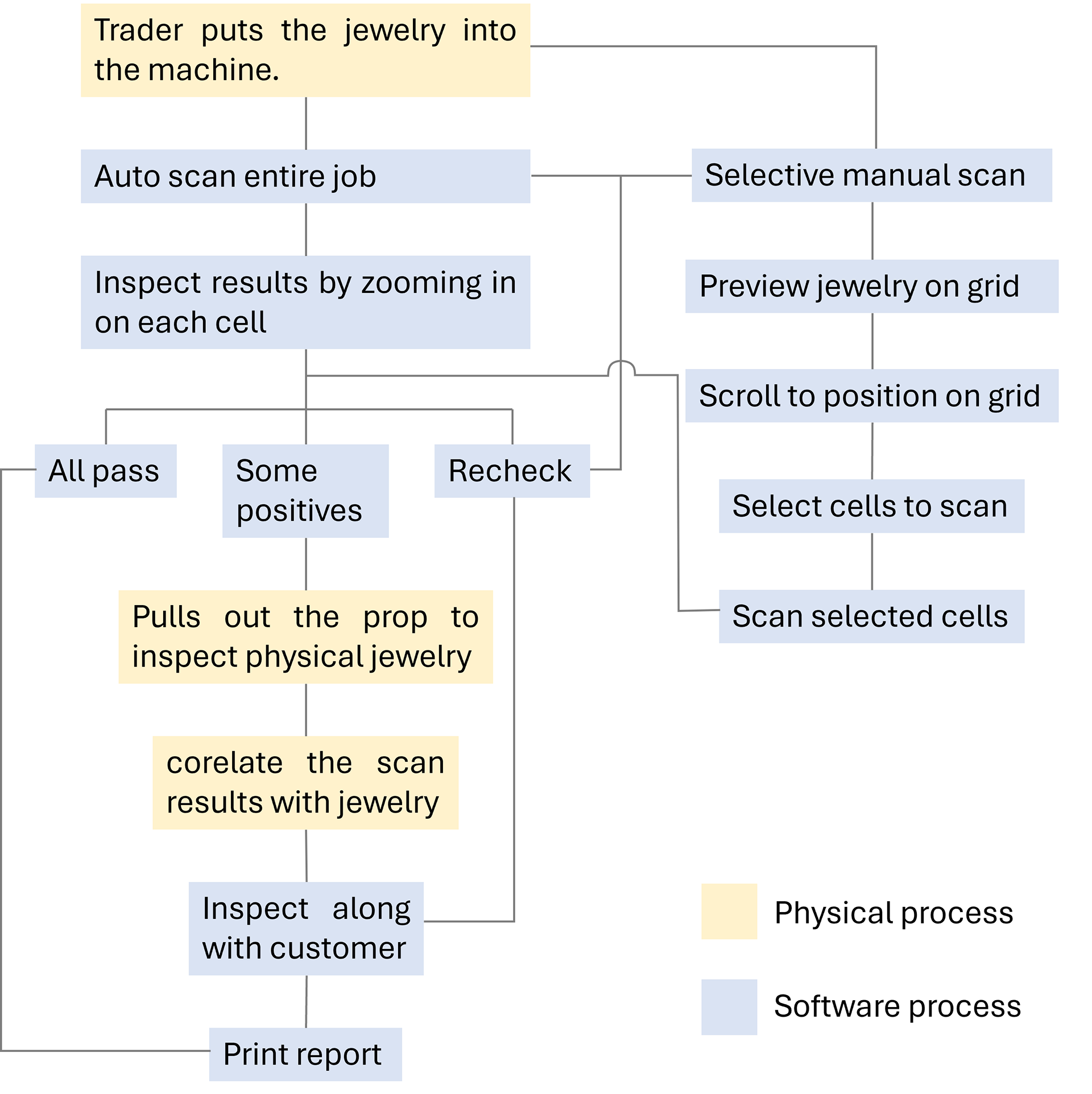
INTERFACE REQUIREMENTS
I then gathered all the different interface functions that I needed to design for. The ones highlighted in blue were unique to this interface.
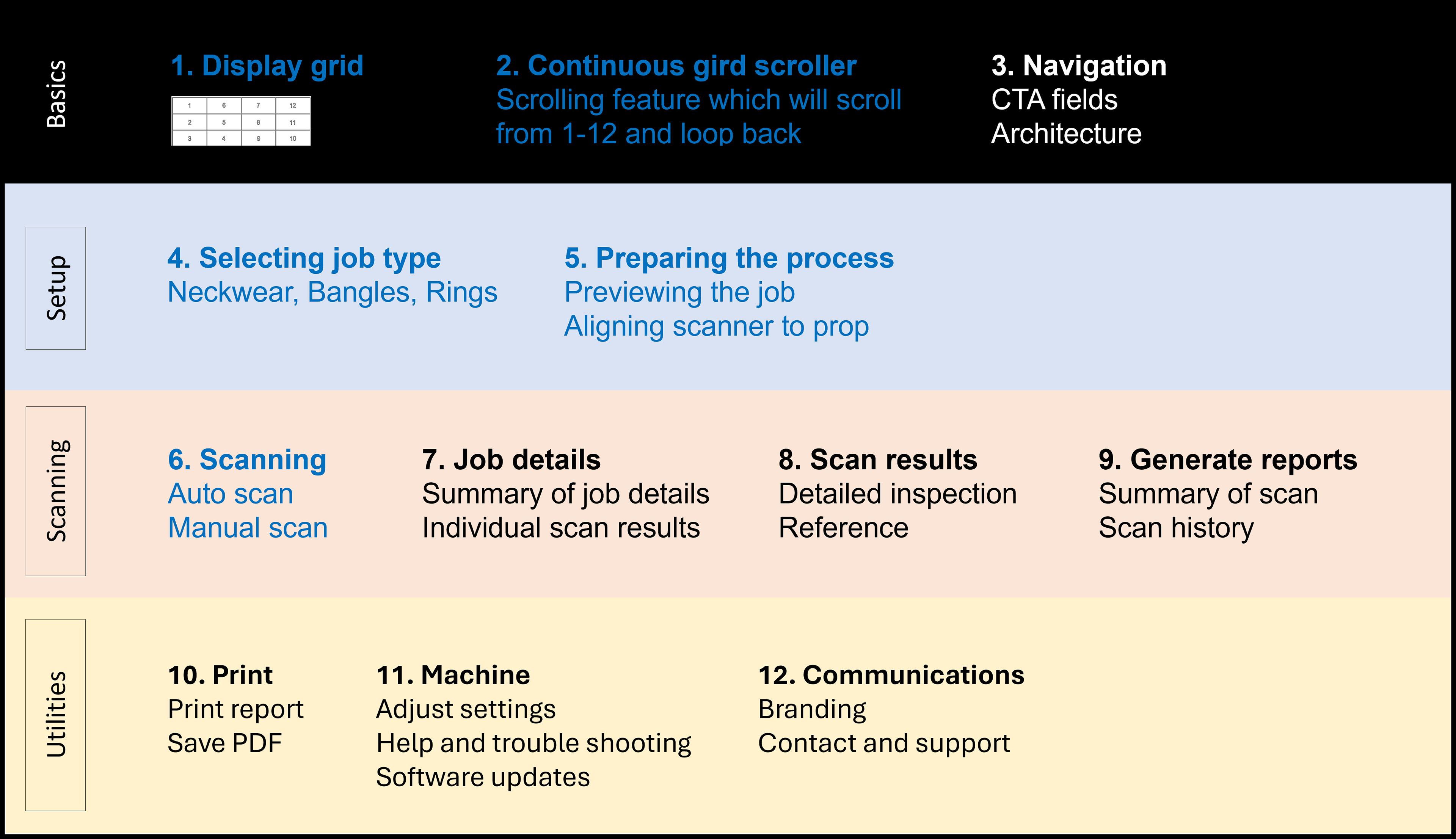
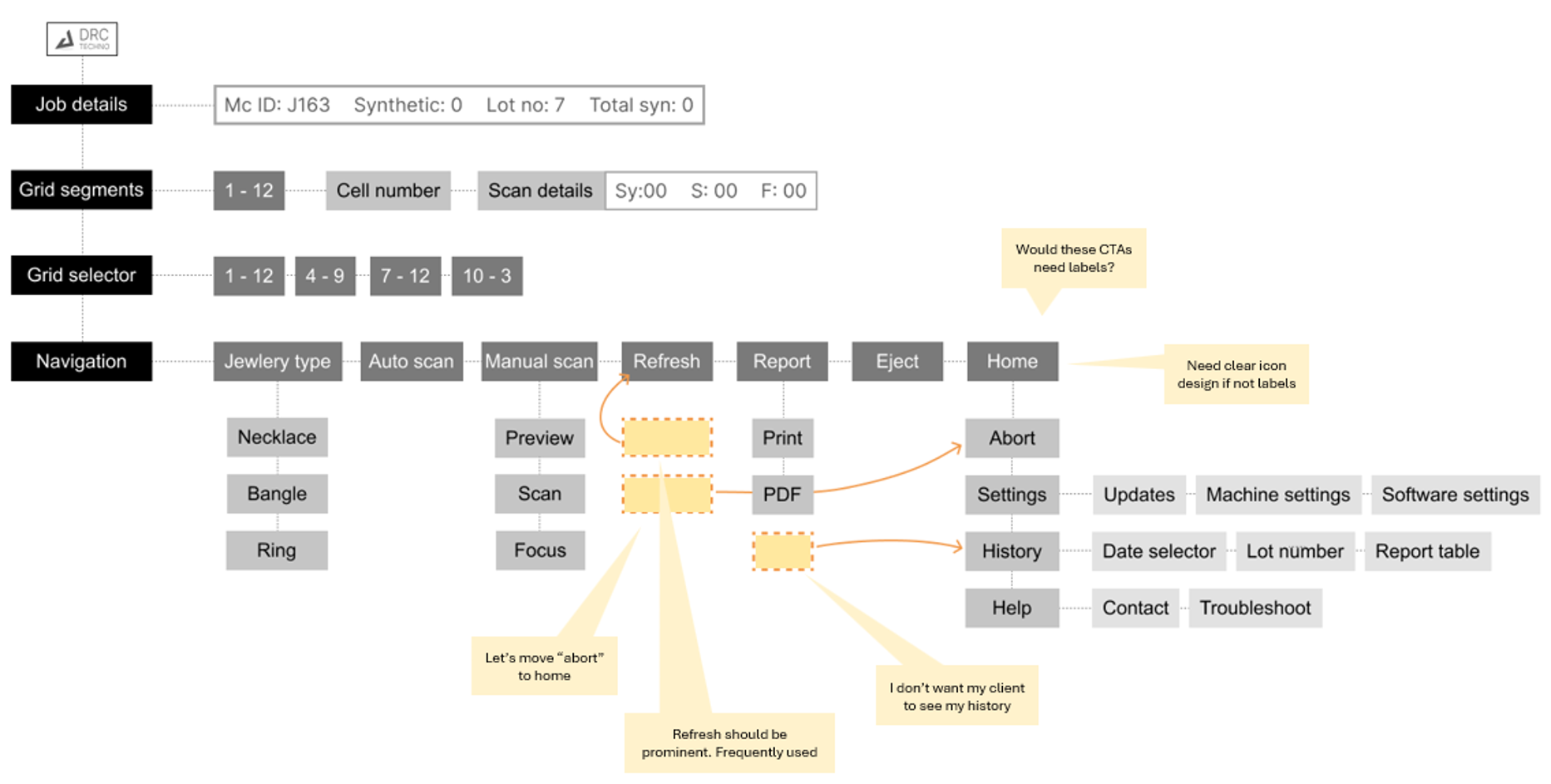
After validating the key features of the product – We discussed the architecture with the clients team and finalized on this architecture which was wide enough for speed of operation but also shallow enough for new users to learn the layout.
FINAL INTERFACE
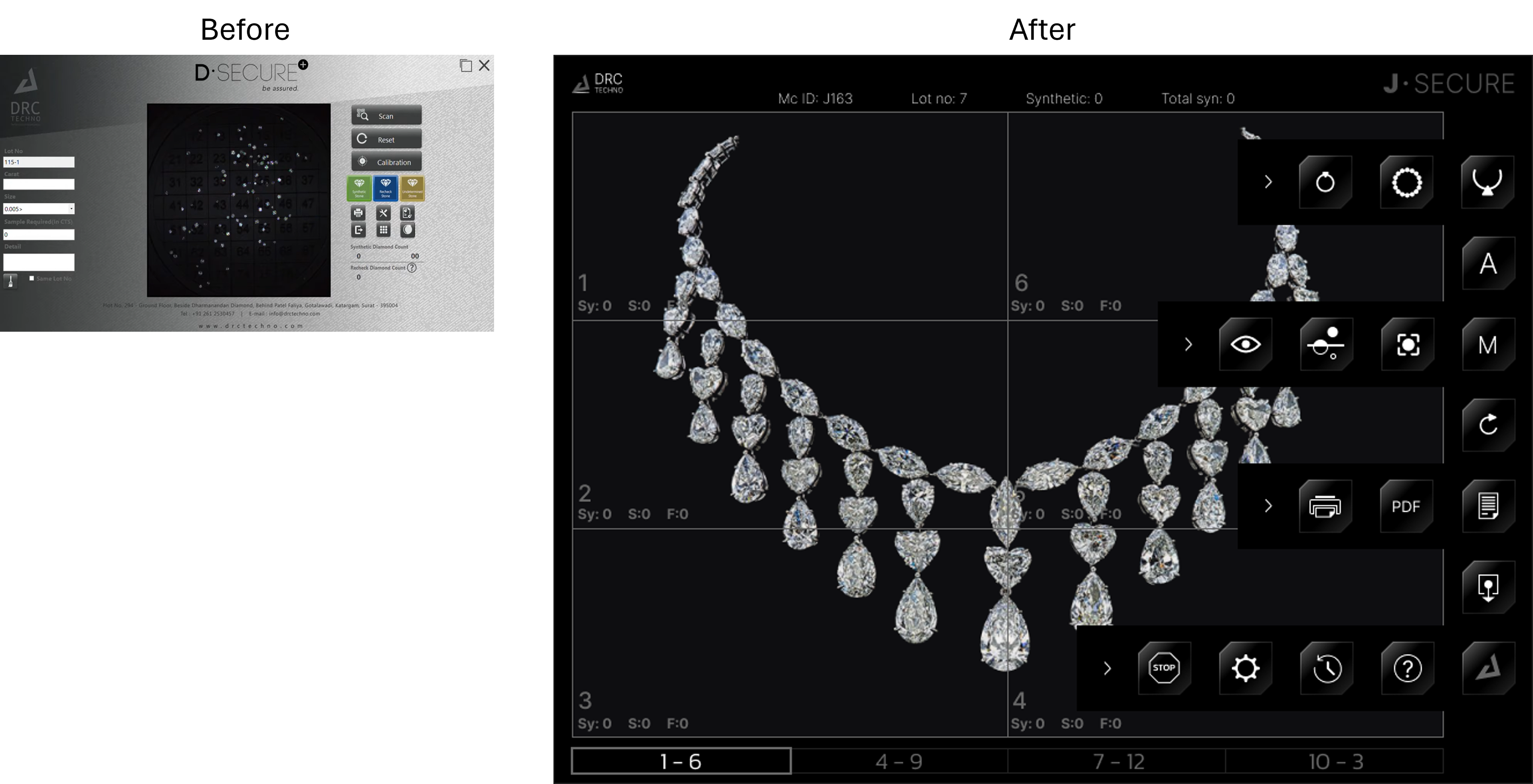
This was the final proposed interface, and you can see the before and after, with a much cleaner and consistent design.
INTERFACE LAYOUT
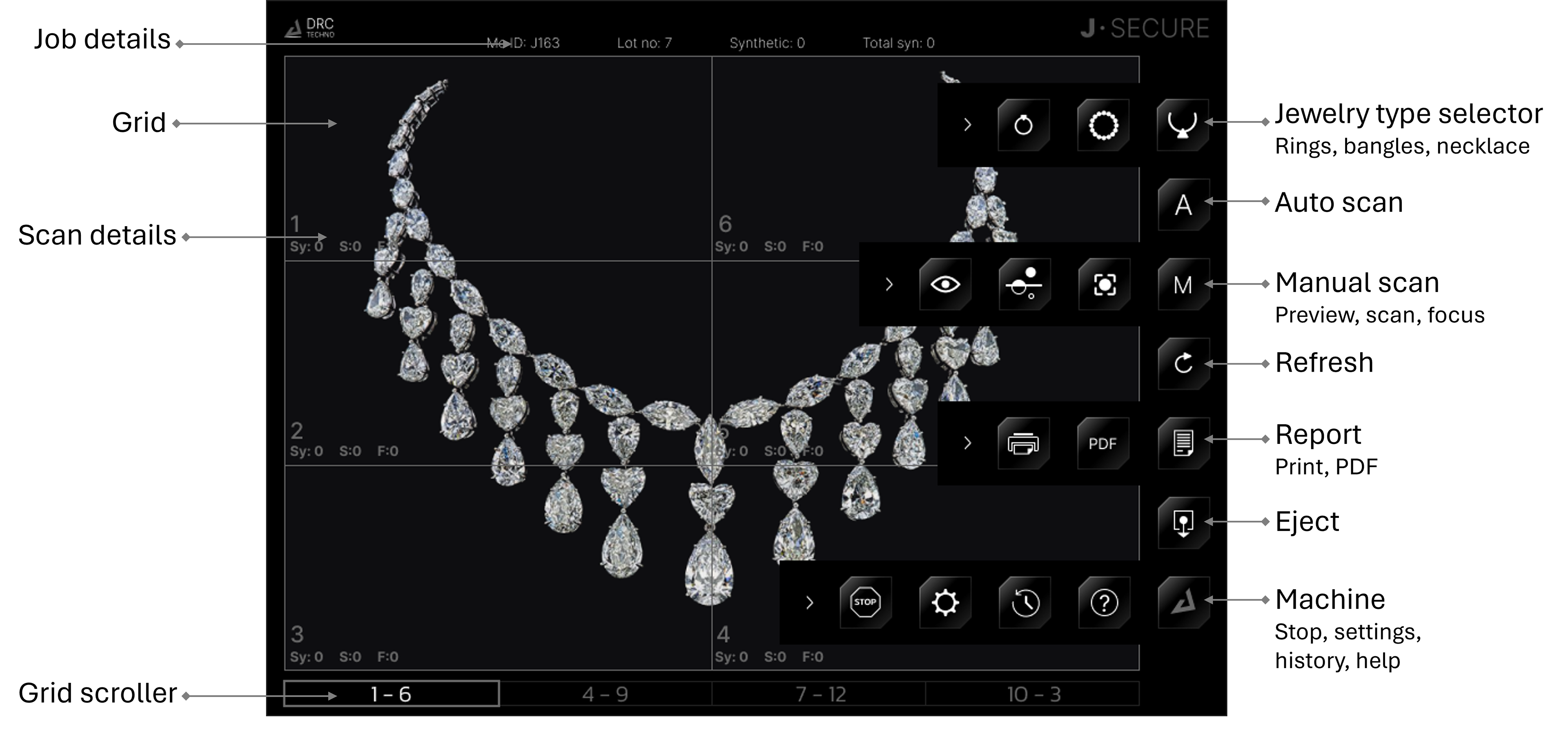
Right on top, you have your job details which update automatically after each scan.
Overlaid on each cell of the grid is the cell number along with the scan details, which are greyed out until you make a scan, and then they display color-coded information.
Overlaid on each cell of the grid is the cell number along with the scan details, which are greyed out until you make a scan, and then they display color-coded information.
At the bottom is the grid scroll function, and the cta field is aligned to the right.
GRID LAYOUT
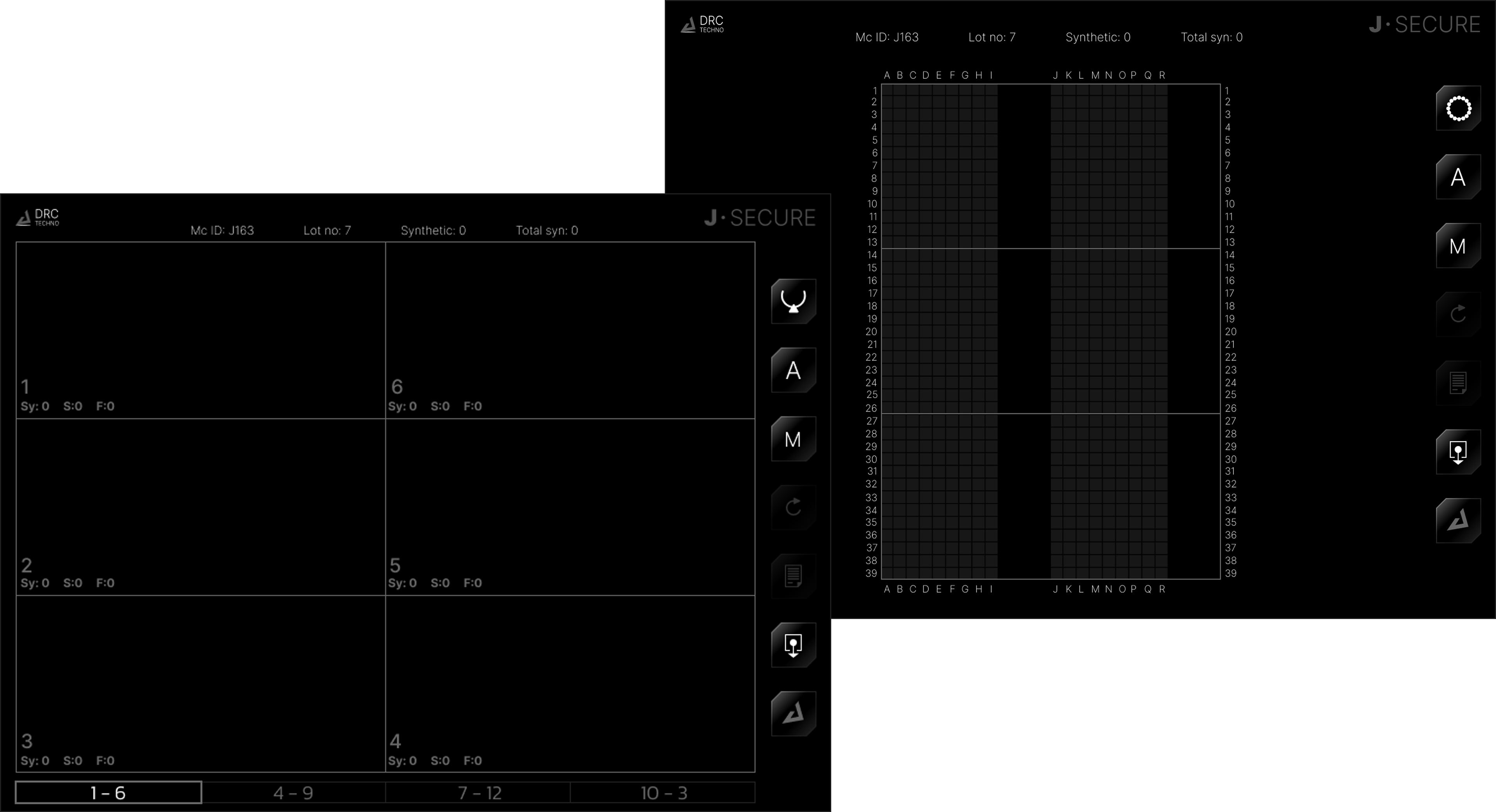
And you have 2 different grids for larger jewelry like necklaces and chockers and a higher resolution grid for bangles and bracelets.
FLOWS - PHYSICAL
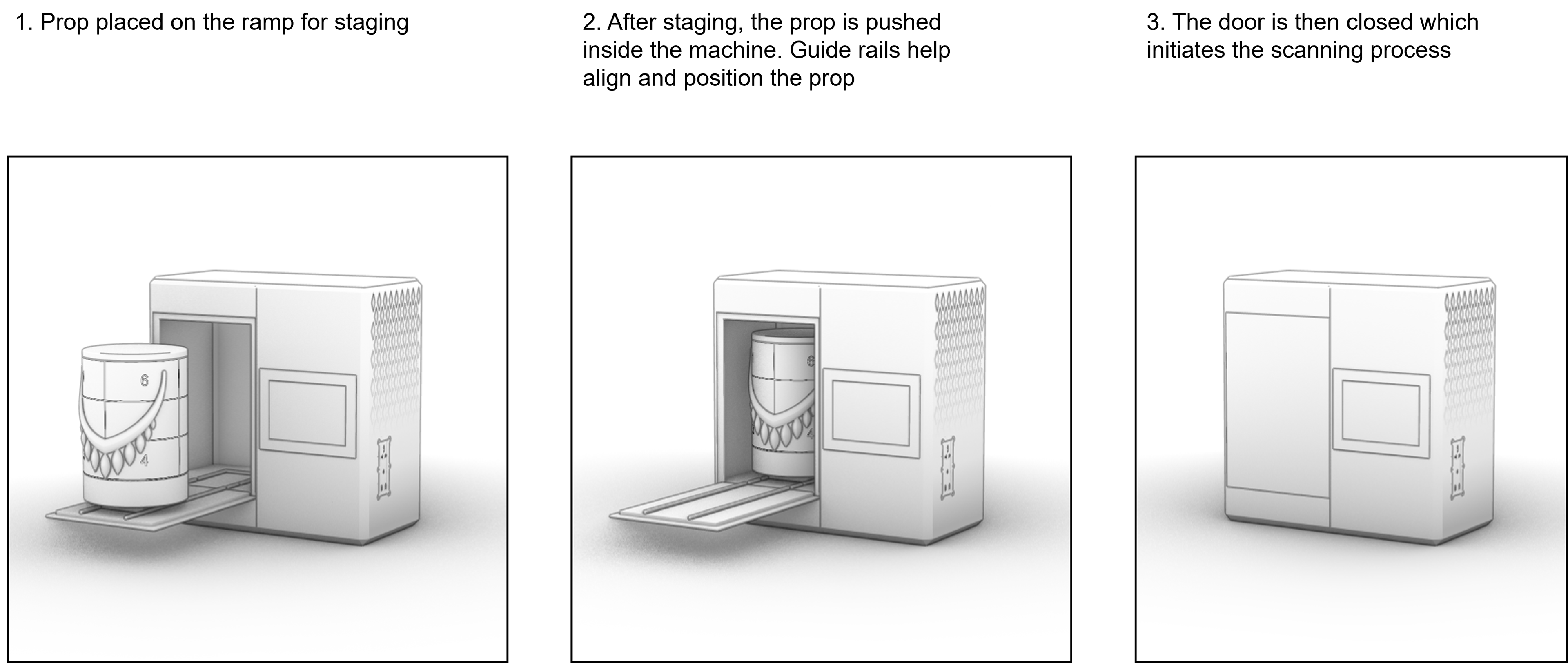
FLOWS - INTERFACE
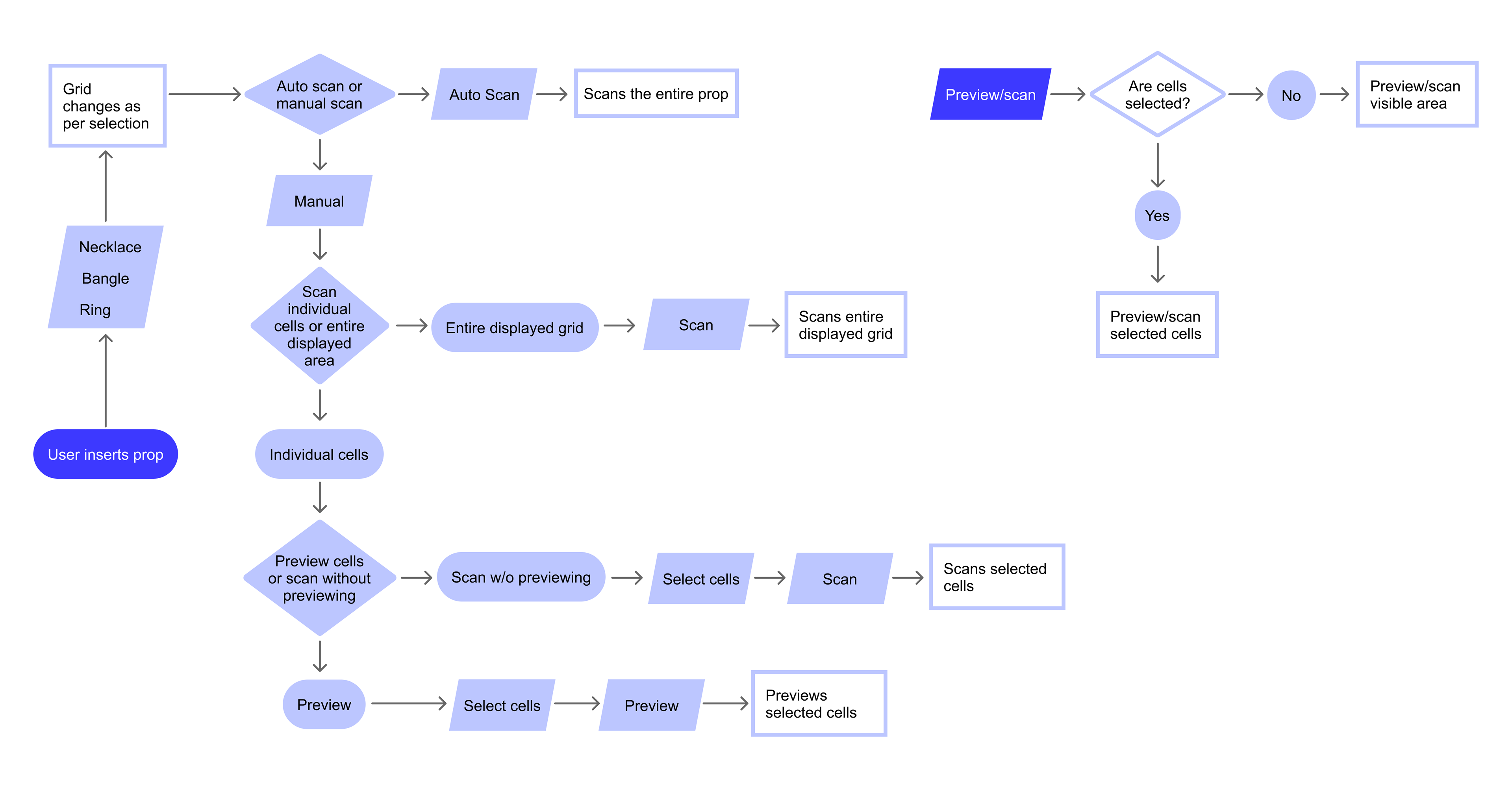
SELECT JEWELRY TYPE TO SCAN
First step is to select the type of jewelry before scanning. The interface adjusts the grid accordingly to match the prop.
AUTOSCAN
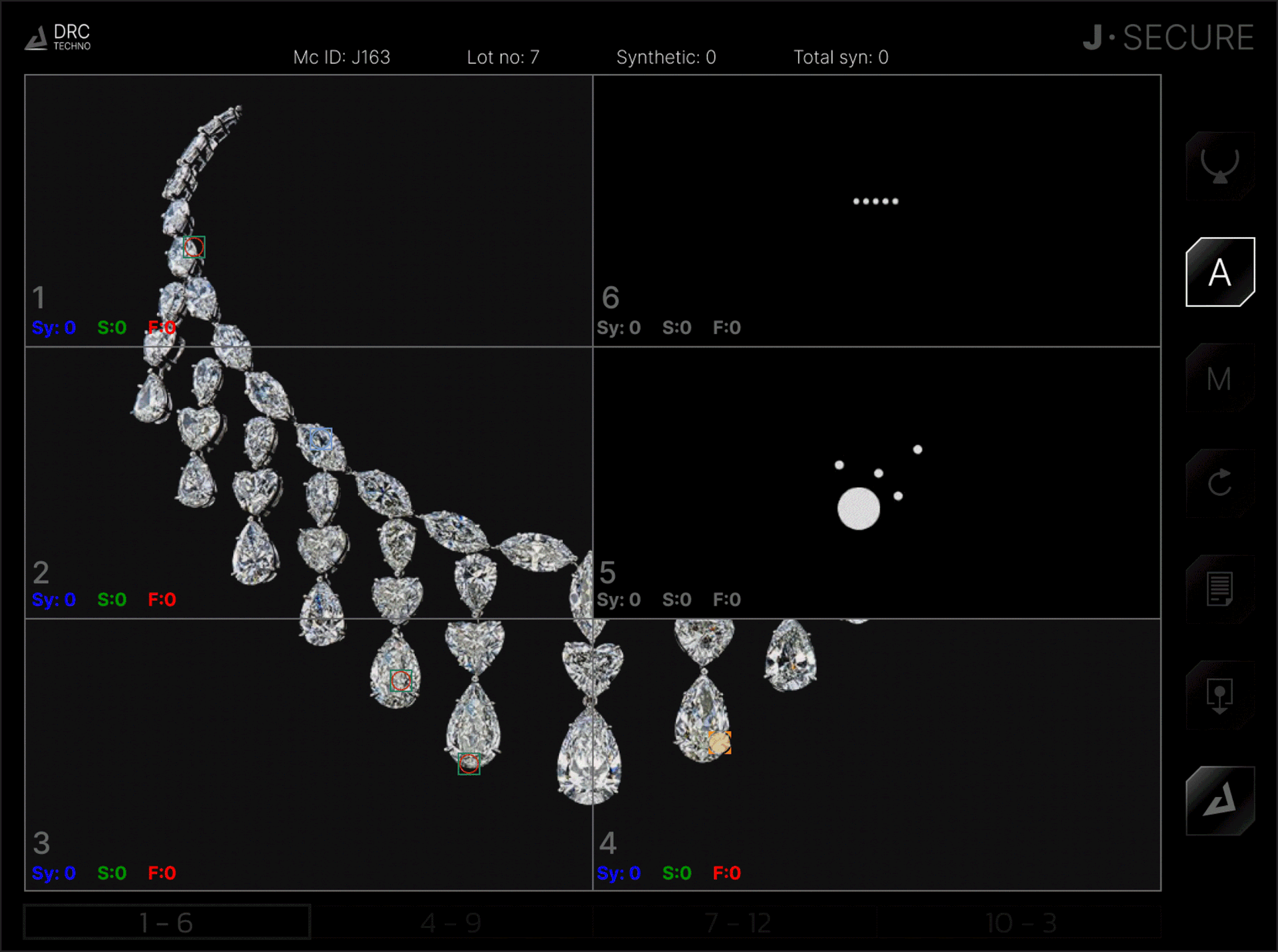
Autoscan to scan the entire prop at once
MANUAL SCAN
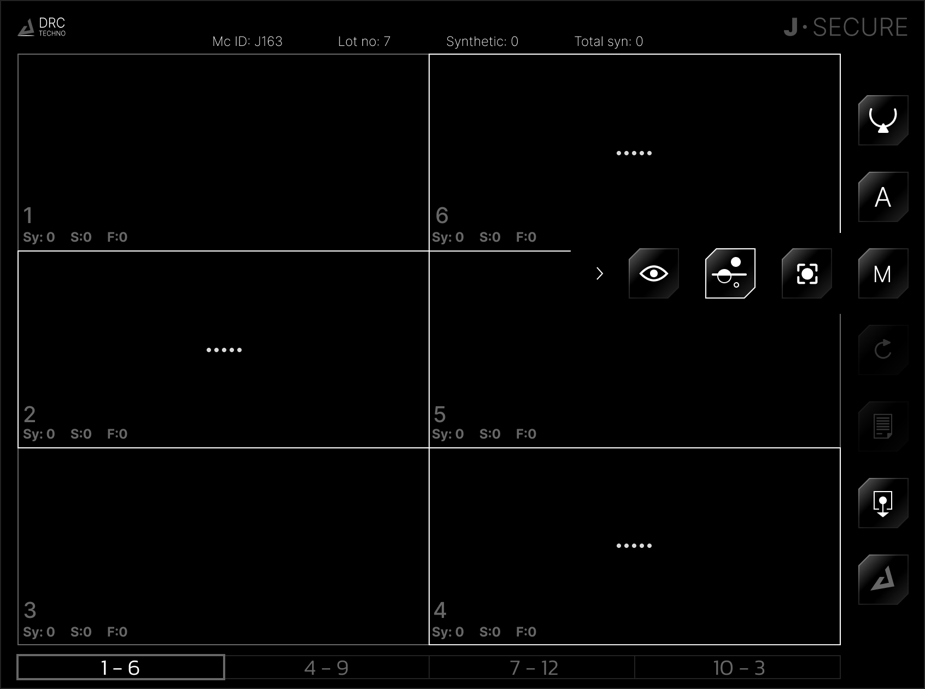
Select cells to scan
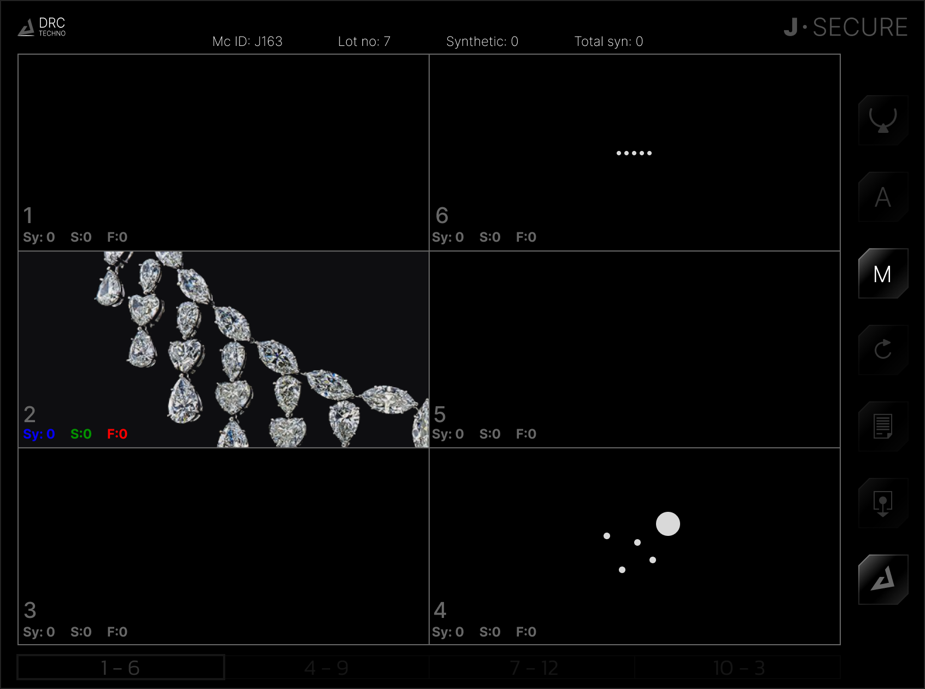
Select manual scan
POST SCAN - INSPECT SCAN
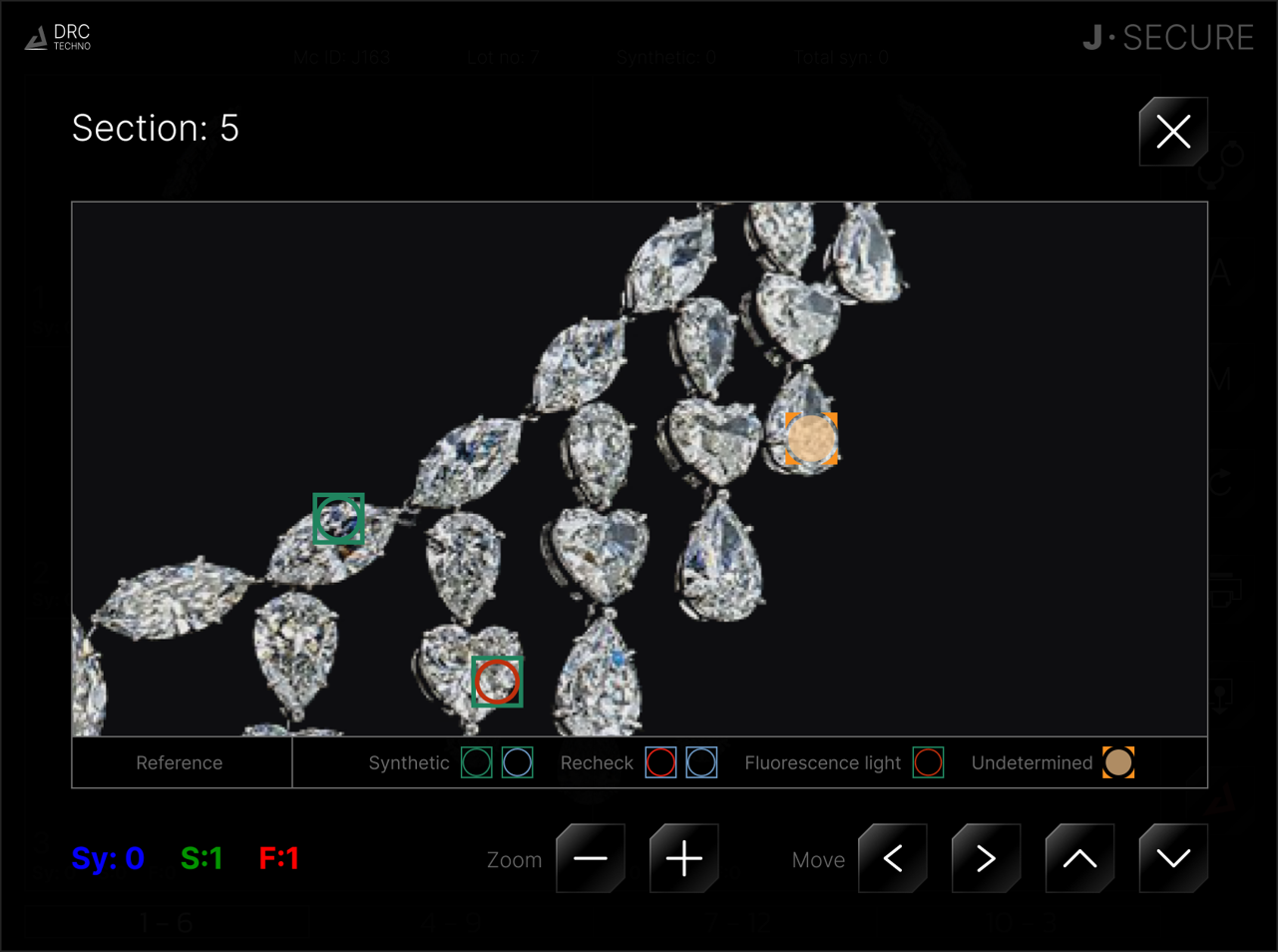
After scanning is complete, each cell can be expanded to examine it closer. Scanning symbols with labels are included below for reference.
POST SCAN - REPORT HISTORY
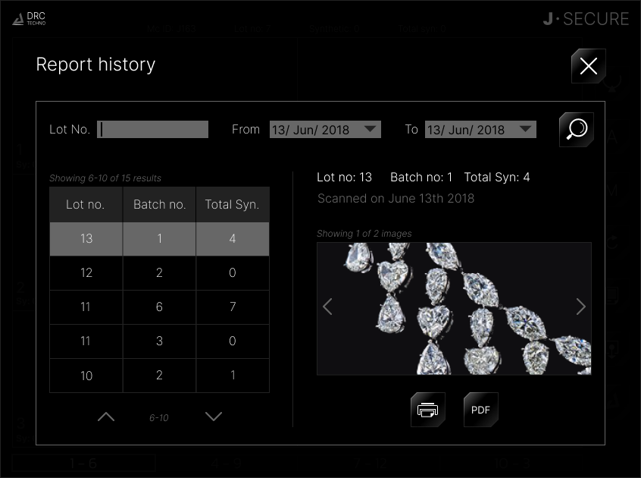
Report history displays a tabular list of scans. Scans can be queried either by lot number or from a date range.
DESIGN HANDOFF

Handoff document with colors, UI components and interaction flows